Understanding rubber gaskets' hardness is crucial for ensuring optimal performance in various applications. The hardness of rubber gaskets is primarily measured using two scales: Shore A and International Rubber Hardness Degrees (IRHD).
This article explores the significance of hardness in rubber gaskets, how it is measured, and the implications for industries relying on these essential components.
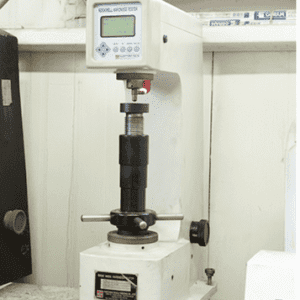
What is the hardness of rubber gaskets?
The hardness of rubber gaskets is primarily measured using the Shore A scale, which quantifies the material's resistance to indentation. This measurement is crucial for determining the suitability of rubber gaskets in various applications, as it directly impacts their sealing effectiveness and durability.
Understanding Rubber Hardness
Rubber hardness is expressed in degrees on the Shore A scale, typically ranging from 40A (soft) to 90A (very hard). Commonly used rubber materials for gaskets include:
- Neoprene: Generally around 60A.
- Nitrile: Also commonly found at 60A.
- EPDM: Typically around 60A.
- Viton: Often rated at about 75A.
- SBR (Red Rubber): Usually falls between 75A and 80A.
Molded rubber products can be found in a broader range, from as low as 20A to as high as 90A. The hardness tolerance is generally ±5 points, meaning a gasket rated at 70A may measure between 65A and 75A without compromising its functionality.
Why Hardness Matters in Rubber Gaskets
Rubber gaskets are widely used in industries such as automotive, aerospace, and manufacturing. The hardness of these gaskets affects several key performance factors:
- Seal Integrity: Hardness influences how well a gasket can maintain a seal under pressure and temperature variations.
- Durability: Softer materials may wear out faster, while harder materials may resist deformation better.
- Compatibility: Different applications may require specific hardness levels to ensure compatibility with fluids or gases.
Measuring Hardness: Shore A vs. IRHD
Shore A Hardness
The Shore A scale is the most commonly used method for measuring the hardness of rubber gaskets. It utilizes a durometer, which consists of a spring-loaded indenter that penetrates the rubber surface. The depth of this indentation correlates with the material's hardness.
- Scale Range: Typically ranges from 0 to 100, with softer materials falling below 40A and harder materials exceeding 90A.
- Common Values: Most rubber gaskets made from Neoprene, Nitrile, and EPDM are around 60A.
IRHD Hardness
IRHD measures hardness using a spherical indenter that applies both minor and major loads to the rubber surface. This method is particularly useful for assessing softer materials or finished products.
- Measurement Process: The depth of indentation is measured after applying a specific load, making it less prone to operator error compared to Shore A.
- Standardization: Governed by ISO standards, IRHD provides a reliable means of comparing different rubber products.
Comparison of Measurement Techniques
Feature | Shore A | IRHD |
---|---|---|
Indenter Type | Spring-loaded cone | Spherical |
Measurement Method | Depth of indentation | Load-based indentation |
Typical Applications | General-purpose gaskets | Soft gaskets and O-rings |
Destructive Testing | Yes (permanent indentation) | No (non-destructive) |
Standard Thickness | 6 mm | 2 mm (for micro tests) |
Interpreting Hardness Values
Understanding how to interpret hardness values is essential for selecting the right gasket material:
- Tolerance Levels: Hardness measurements typically have a tolerance of ±5 points. For instance, a gasket rated at 70A could measure anywhere from 65A to 75A.
- Material Selection: Knowing the hardness helps in choosing materials that will withstand specific operational conditions, such as temperature fluctuations or exposure to chemicals.
Choosing the Right Hardness for Your Rubber Gaskets
When selecting rubber gaskets for your application, it's crucial to consider the following factors:
Application Type
- Static Seals: For applications where there's minimal movement, harder gaskets can be sufficient. They offer better resistance to compression and provide a reliable seal.
- Dynamic Seals: For applications involving movement or vibration, softer gaskets are generally preferred. They can accommodate changes in surface contact and reduce friction.
Surface Conditions
- Rough or Uneven Surfaces: Softer materials can effectively fill gaps and irregularities on rough surfaces, ensuring a proper seal.
Pressure and Temperature Requirements
- High Pressure: Harder materials can better withstand high pressure without deforming, preventing leaks.
- Temperature Extremes: Choose rubber compounds that can maintain their hardness and properties under both high and low temperatures.
Here's a quick reference table to summarize the key factors:
Application Type | Surface Conditions | Pressure | Temperature | Recommended Hardness |
---|---|---|---|---|
Static Seals | Smooth | Low | Moderate | Hard |
Static Seals | Rough | Low | Moderate | Soft |
Dynamic Seals | Smooth | Moderate | Moderate | Medium |
Dynamic Seals | Rough | Moderate | Moderate | Soft |
High Pressure | Smooth | High | Moderate | Hard |
High Temperature | Smooth | Moderate | High | Heat-resistant |
Low Temperature | Smooth | Moderate | Low | Cold-resistant |
These are general guidelines. Specific applications may require more in-depth analysis and testing to determine the optimal hardness. Consult with a rubber specialist or gasket manufacturer for expert advice.
Conclusion
The hardness of rubber gaskets plays a vital role in their performance across various applications. By utilizing both Shore A and IRHD measurement techniques, industries can ensure they select the appropriate gasket material that meets their specific needs. Understanding these measurements not only aids in quality control but also enhances product reliability, ultimately leading to better operational efficiency. For businesses looking to optimize their gasket selection process or seeking further insights into rubber material properties, consulting with experts in gasket manufacturing can provide tailored solutions that address unique challenges and requirements.
Would you like to discuss a specific application or have any other questions about rubber gaskets?
Contact us today to get more information!