When selecting rubber materials for outdoor applications, UV resistance is a critical factor. Prolonged exposure to ultraviolet (UV) light can degrade many types of rubber, leading to loss of flexibility, strength, and overall integrity. This article explores the best rubber options for UV resistance, comparing various materials and their applications in industrial settings.
Understanding UV Resistance in Rubber
UV radiation affects the molecular structure of rubber, causing it to break down over time. The degradation process can lead to cracking, fading, and eventual disintegration of the material. Therefore, choosing the right rubber for applications exposed to sunlight is essential for ensuring longevity and performance.
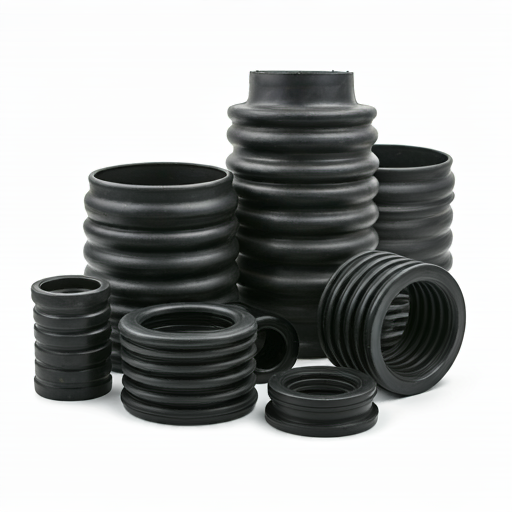
Top UV-Resistant Rubber Materials
- EPDM (Ethylene Propylene Diene Monomer)
- Overview: EPDM is widely recognized for its superior UV resistance and weathering properties. It remains flexible and durable even under harsh environmental conditions.
- Applications: Commonly used in roofing systems, automotive seals, and gaskets.
- Advantages:
- Excellent ozone and UV resistance
- High-temperature stability
- Good tensile strength
- Disadvantages: Limited resistance to oil and certain chemicals.
- Silicone Rubber
- Overview: Silicone rubber boasts outstanding UV stability and can withstand extreme temperatures without losing its properties.
- Applications: It is ideal for electrical insulations, automotive seals, and medical devices.
- Advantages:
- Exceptional UV and temperature resistance
- Maintains flexibility over a wide temperature range
- Disadvantages: Generally more expensive than other rubber types.
- Viton (Fluoroelastomer)
- Overview: Viton, a fluoroelastomer, is highly resistant to extreme temperatures, chemicals, and oils. It maintains its performance in harsh environments.
- Applications: Used in automotive seals, aerospace components, and chemical processing equipment.
- Advantages:
- Excellent resistance to high temperatures, oils, and chemicals
- Good mechanical strength and durability
- Low flammability
- Disadvantages:
- Higher cost compared to other elastomers
- Limited flexibility at low temperatures
- Neoprene
- Overview: Neoprene offers good UV resistance along with durability against oil and chemicals.
- Applications: Commonly used in wetsuits, seals, and gaskets.
- Advantages:
- Reasonable UV resistance
- Good mechanical properties
- Disadvantages: Degrades faster than EPDM or silicone under prolonged UV exposure.
- Butyl Rubber
- Overview: Butyl rubber is renowned for its exceptional impermeability to gases, making it ideal for applications requiring airtight seals. It exhibits excellent resistance to aging and weathering.
- Applications: Widely used in inner tubes, tire valves, and sealing gaskets.
- Advantages:
- Outstanding gas impermeability
- Excellent resistance to aging and weathering
- Good electrical insulation properties
- Disadvantages:
- Poor resistance to heat and sunlight
- Limited flexibility at low temperatures
Materials with Poor UV Resistance
- Nitrile Rubber (Buna-N): While excellent for oil resistance, nitrile deteriorates quickly under UV exposure.
- Natural Rubber: Prone to rapid degradation when exposed to sunlight; not recommended for outdoor use.
Comparative Analysis of UV-Resistant Rubbers
Material | UV Resistance | Temperature Range | Chemical Resistance | Common Applications |
---|---|---|---|---|
EPDM | Excellent | -40°C to 121°C | Good | Roofing, seals |
Silicone | Excellent | Up to 260°C | Excellent | Automotive seals, gaskets |
Viton | Very Good | -26°C to 230°C | Excellent | Aerospace seals |
Neoprene | Moderate | -40°C to 120°C | Good | Automotive parts |
Butyl | Good | -45°C to 121°C | Good | Liners, sealants |
Nitrile | Poor | Varies | Excellent | Oil seals (not outdoors) |
Natural Rubber | Poor | Varies | Moderate | General use (not outdoors) |
How to choose the right rubber material for UV resistance
Selecting the right rubber material for UV resistance depends on the specific requirements of your application. Each type of rubber has unique properties that make it suitable for different environments and challenges. Here, we’ll explore additional considerations to help you make an informed decision.
Key Considerations for Choosing UV-Resistant Rubber
- Environmental Exposure:
- Assess the level of UV exposure your rubber products will face. For applications in direct sunlight, such as roofing or outdoor seals, materials like EPDM and silicone are recommended due to their superior UV resistance.
- Temperature Range:
- Consider the operating temperature of your application. Silicone rubber excels in extreme temperatures, making it ideal for high-heat environments, while EPDM performs well in a broader range of temperatures.
- Chemical Compatibility:
- If your application involves exposure to oils or chemicals, rubber types like nitrile or neoprene may be more appropriate. Ensure that the selected rubber is compatible with any substances it will contact.
- Mechanical Properties:
- Evaluate the mechanical demands of your application. Consider tensile strength, elongation, and abrasion resistance. EPDM and silicone offer excellent mechanical properties suitable for a variety of demanding applications.
- Cost and Availability:
- Budget constraints can influence your choice. While silicone offers the best performance, it may be more expensive than EPDM or neoprene. Analyze your project’s budget to find a balance between performance and cost.
Testing and Validation
Before finalizing your choice, it's advisable to conduct tests to validate the rubber's performance in your specific application conditions. This may include:
- Accelerated Aging Tests: To assess how the rubber material withstands UV exposure over time.
- Mechanical Testing: To evaluate how the material performs under stress and strain.
- Chemical Resistance Testing: To ensure compatibility with any substances the rubber may encounter.
Conclusion
Choosing the right rubber material for UV resistance is critical for ensuring the longevity and performance of your products. By considering environmental exposure, temperature ranges, chemical compatibility, mechanical properties, and cost, you can make a well-informed decision. Always prioritize testing to confirm that your selected material meets the specific requirements of your application.
Ready to enhance the durability of your products against UV radiation? Contact us today for expert guidance on selecting the ideal rubber material for your needs. Our extensive inventory and knowledgeable team are here to support you in achieving optimal performance in your industrial applications!