Materials of Excellence
Crafting with the Best in the Business
At Julong Rubber, we prioritize using the finest materials to ensure the durability, efficiency, and performance of every product. Explore the various high-quality materials that form the foundation of our premium rubber components.
Ethylene Propylene Diene Monomer (EPDM)
EPDM rubber is one of the most versatile synthetic rubbers in the industry. Known for its outstanding resistance to weather, ozone, and aging, it’s a top choice for outdoor applications, roofing, seals, and more. But how does it compare to NBR or other rubber materials?
EPDM, or Ethylene Propylene Diene Monomer rubber, is a synthetic elastomer recognized for its excellent weather resistance, UV stability, and durability in extreme temperatures. It’s widely used in automotive seals, roofing membranes, and drinking water systems.
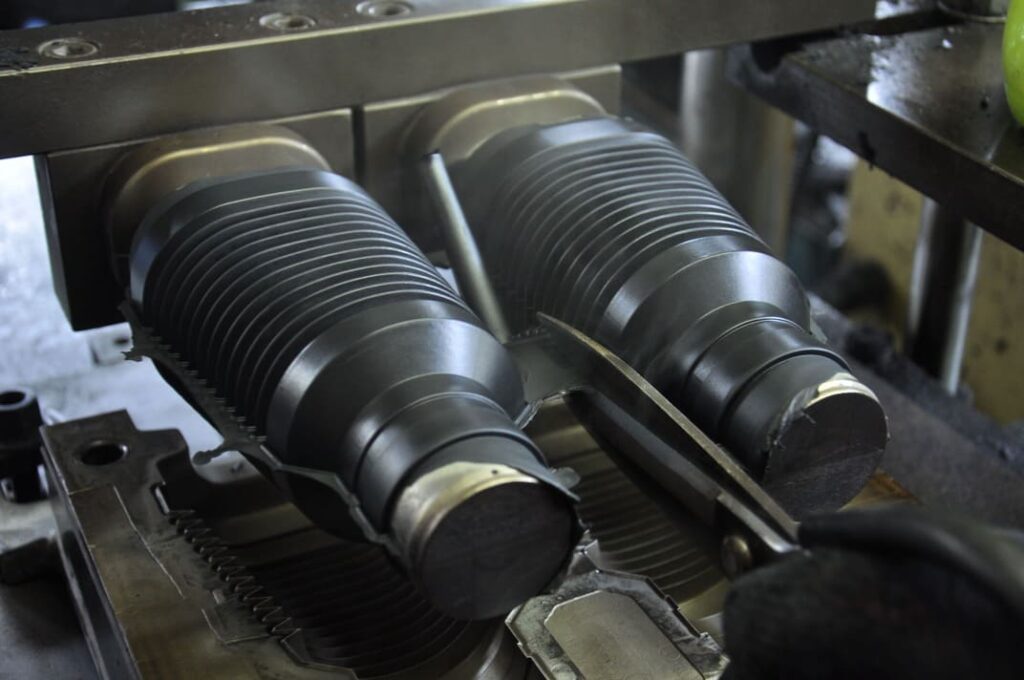
What is EPDM or Ethylene Propylene Diene Monomer?
EPDM is a synthetic rubber made by copolymerizing ethylene, propylene, and a diene monomer. The inclusion of the diene allows for cross-linking via sulfur vulcanization, which enhances flexibility and resistance to outdoor elements.
EPDM is a high-performance rubber designed for excellent resistance to weathering, ozone, UV rays, and aging. It performs well across a wide temperature range from -50°C to +150°C.
🔬 Chemical Structure
- Ethylene + Propylene + Diene = EPDM
- The diene component introduces unsaturation, allowing vulcanization and improved properties.
What are the Raw Materials of EPDM?
- Ethylene (C2H4): Provides strength and stability.
- Propylene (C3H6): Adds flexibility and weather resistance.
- Diene (commonly ENB – Ethylidene Norbornene): Enables vulcanization and crosslinking, improving elasticity and durability.
What is the Characteristic of EPDM?
✅ Characteristic | 🔍 Details |
---|---|
🌦️ Weather Resistance | Outstanding resistance to UV, ozone, and aging. |
💧 Water Resistance | Excellent resistance to water and steam. |
🌡️ Temperature Range | Performs between -50°C to +150°C. |
🧪 Chemical Resistance | Resists polar substances like acids and alkalis. |
⚡ Electrical Insulation | Good dielectric properties. |
What are the Two Types of EPDM?
- Sulfur-Cured EPDM
✅ Lower cost, faster curing time.
❌ Limited heat resistance (up to 130°C). - Peroxide-Cured EPDM
✅ Better heat and chemical resistance (up to 150°C).
✅ Preferred for drinking water applications.
What are the Advantages and Disadvantages of EPDM?
🏆 Advantages
- 🌞 Exceptional UV and ozone resistance
- 🌧️ Excellent water and steam resistance
- ❄️ Wide temperature tolerance (-50°C to +150°C)
- ⚡ Excellent electrical insulation properties
- ♻️ Eco-friendly and compliant with drinking water regulations
⚠️ Disadvantages
- 🛢️ Poor oil and fuel resistance
- ⚗️ Not compatible with hydrocarbons and petroleum products
- 🧵 Lower tear strength in dynamic applications compared to NBR or FKM
What is Ethylene Propylene Rubber Used For?
EPDM is used in automotive weather seals, roofing membranes, garden hoses, drinking water seals, and insulation materials.
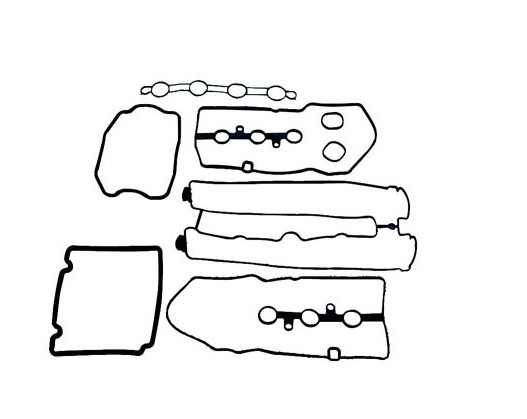
🏗️ 1. Construction and Roofing Industry
🚗 2. Automotive Industry
- ✅ Door and Window Seals: Prevents water leaks and reduces noise in vehicle cabins.
- ✅ Radiator Hoses: EPDM’s heat and chemical resistance make it suitable for engine cooling systems.
- ✅ Weatherstripping: Seals the vehicle’s exterior components to protect against dust, water, and noise.
🏭 3. HVAC Industry (Heating, Ventilation, and Air Conditioning)
- ✅ Gaskets and Seals: Used in HVAC duct systems to prevent air leaks.
- ✅ Insulation Jacketing: EPDM rubber sheets cover insulation materials to protect against moisture and UV rays.
- ✅ Flexible Connectors: Reduce noise and vibration in HVAC systems.
🔌 4. Electrical and Cable Industry
- ✅ High Voltage Cable Insulation: EPDM’s electrical resistance makes it ideal for insulation in power cables.
- ✅ Cable Jacketing: Provides a protective barrier against moisture, UV, and chemicals.
🌊 5. Marine Industry
- ✅ Hatch Seals: Ensures water-tight integrity in boat hatches and portholes.
- ✅ Fendering Systems: EPDM absorbs impact, protecting vessels during docking.
- ✅ Marine Hoses: Resistant to saltwater and UV, ideal for bilge pump and exhaust hoses.
🔧 EPDM Applications Performance Comparison Table
Industry | Primary Applications | Operating Temp. (°C) | Key Benefits | Challenges |
---|---|---|---|---|
Construction | Roofing membranes, expansion joints | -40 to +150 | UV and ozone resistance | Low oil resistance |
Automotive | Seals, hoses, weatherstripping | -50 to +125 | Weatherproofing, flexibility | Not compatible with petroleum oils |
HVAC | Duct seals, insulation jacketing | -40 to +150 | Heat and moisture resistance | Limited resistance to hydrocarbons |
Electrical | Cable jacketing, insulation | -50 to +125 | Electrical resistance, UV stability | Not suitable for fuel exposure |
Marine | Hatch seals, fendering systems | -40 to +120 | Saltwater and UV resistance | Limited solvent resistance |
What is EPDM Not Compatible With?
❌ Substance | ⚠️ Why Not? |
---|---|
Petroleum-based oils | Causes swelling and material breakdown |
Fuels (Gasoline/Diesel) | Leads to degradation and failure |
Aromatic hydrocarbons | Attacks the polymer backbone |
Is EPDM Safe for Drinking Water?
✅ Yes! EPDM rubber is certified for drinking water applications. It complies with NSF/ANSI 61, WRAS, and KTW standards for potable water safety.
Is EPDM UV Resistant?
✅ Absolutely! EPDM rubber has excellent UV and ozone resistance, making it ideal for outdoor applications like roofing membranes, window seals, and water hoses.
How to Identify EPDM Rubber?
- 🧐 Black or white color with a smooth matte surface
- 🔥 Burn test: Burns with little smoke and faint sweet smell
- 🧪 Resistant to water and steam, but fails in oil resistance tests
Which is Better, Viton or EPDM?
🔍 Feature | 🏆 EPDM | 🏆 Viton (FKM) |
---|---|---|
UV/Ozone Resistance | ✅ Excellent | ✅ Excellent |
Water Resistance | ✅ Excellent | ❌ Poor |
Oil/Fuel Resistance | ❌ Poor | ✅ Excellent |
Temperature Range | -50°C to +150°C | -20°C to +230°C |
Cost | Lower | Higher |
How Long Does EPDM Rubber Last?
🌎 Environment | ⏳ Expected Lifespan |
---|---|
Indoor Applications | ✅ 15+ years |
Outdoor Applications | ✅ 20-25 years |
Roofing Membranes | ✅ 30+ years |
🔧 Tips to Maximize EPDM Longevity
- ✅ Avoid contact with petroleum oils
- ✅ Regular maintenance and inspection
- ✅ Use proper installation methods
🔍 Conclusion
EPDM rubber is a versatile, durable material perfect for outdoor, automotive, and water applications. Its superior resistance to UV, ozone, and aging makes it ideal for seals, roofing membranes, and drinking water systems.
However, for applications involving oils or fuels, NBR or FKM are better choices.
📞 Get a Free Quote or Sample of EPDM Products!
Looking for high-quality EPDM rubber seals, gaskets, or custom molded parts? We offer custom solutions tailored to your needs.
- ✅ Free samples available
- ✅ Fast production and delivery
- ✅ ISO & ROHS certified materials
📧 Contact Kelly at Julong Rubber Today!
Email: info@rubberandseal.com
Website: www.rubberandseal.com
🔗 Explore Other Rubber Materials
Custom Rubber Parts with Easy
At Julong Rubber, We turn complex Into Simple! Follow the following 3 steps to start today!

Tell Us What You Need
Tell us as specific as possible of your needs, provide the drawing, reference picture and share your idea.
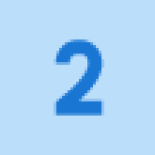
Get Solution & Quote
We will work on the best solution according to your requirements and drawing, the specific quote will be provided within 24 hours.

Approve for Mass Production
We will start mass production after getting your approval and deposit, and we will handle the shipment.
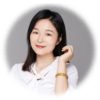
Get A Free Quote
Contact us to get a free quote and more expertise about custom rubber parts. Your project will meet the right solution at Julong Rubber.
Email:info@rubberandseal.com