To make custom rubber parts, manufacturers typically use molding techniques, including injection molding, compression molding, and transfer molding, which shape raw rubber materials into precise parts by heating and pressing in molds.
Custom rubber parts are critical components in industries ranging from automotive to medical, requiring precise specifications to meet performance and durability standards. However, ensuring the right fit, material durability, and cost-efficiency can be challenging due to the vast range of rubber compounds and manufacturing methods available. This guide provides a step-by-step overview of the key processes and materials involved in custom rubber part manufacturing, helping you make informed decisions for your industrial needs.
How Are Custom Rubber Parts Made? Manufacturers create custom rubber parts through several key processes—primarily injection molding, compression molding, and transfer molding. Each method utilizes specific molds and temperatures to shape rubber into the desired part, ensuring optimal durability, flexibility, and performance for various industrial applications.
For companies interested in custom rubber components, choosing the right process can significantly impact the final product's quality, performance, and cost-efficiency.
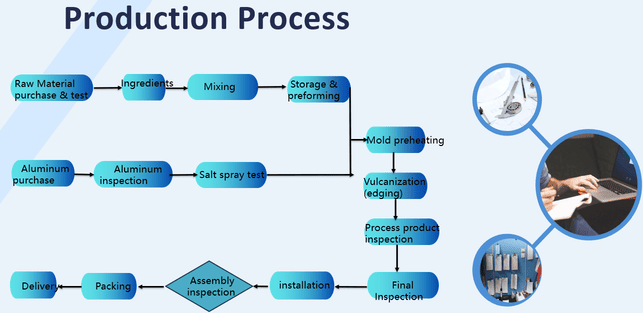
1. Understanding Rubber Materials for Custom Parts
Choosing the correct rubber material is essential for custom part performance. Each type of rubber compound has unique properties:
- Natural Rubber: Known for excellent tensile strength, flexibility, and resilience, natural rubber is ideal for applications requiring wear resistance. However, it has limited resistance to oils and is unsuitable for high-temperature environments.
- Nitrile Rubber: Excellent for oil and fuel resistance, nitrile is widely used in automotive applications. Its durability makes it a top choice for seals and gaskets.
- Silicone Rubber: With a high resistance to heat, silicone is perfect for medical and food-grade applications, as well as components exposed to extreme temperatures.
- Polyurethane Rubber: Known for its toughness and abrasion resistance, polyurethane rubber works well for high-wear industrial applications.
Rubber Type | Key Properties | Best Uses |
---|---|---|
Natural Rubber | Flexibility, tensile strength | Wear-resistant applications |
Nitrile Rubber | Oil and fuel resistance | Automotive seals, gaskets |
Silicone Rubber | Heat resistance, biocompatible | Medical, food-grade components |
Polyurethane | Abrasion resistance, toughness | High-wear industrial parts |
2. Main Techniques for Creating Custom Rubber Parts
Each molding method has advantages depending on the part’s size, complexity and required durability.
- Injection Molding: This method injects molten rubber into a metal mold under high pressure, which allows for high precision and intricate designs. It’s ideal for large production volumes and parts with detailed features.
- Compression Molding: Here, a pre-heated rubber material is placed into a mold cavity and compressed until it takes the mold’s shape. This process is most suitable for simple shapes, larger parts, or lower production volumes.
- Transfer Molding: Similar to compression molding but with greater precision, transfer molding involves pre-forming the rubber and then forcing it into a mold cavity. It’s well-suited for medium-complexity parts and reduces waste.
Molding Method | Best For | Pros |
---|---|---|
Injection Molding | High precision, intricate parts | High accuracy, fast for large volumes |
Compression Molding | Simple, larger parts | Cost-effective for lower volumes |
Transfer Molding | Medium complexity, low waste | Reduces waste, good for complex shapes |
3. Mold Design and Prototyping
Mold design is a crucial step in producing custom rubber parts with precise dimensions and tolerances. Engineers typically use CAD software to create 3D mold designs, which allows them to visualize and test part dimensions. Additionally, 3D printing technology offers an efficient way to create prototypes. Rubber molds can be printed quickly and affordably, making it easy to test the part’s fit and functionality before full production.
4. Quality Control and Testing
For custom rubber parts to meet industry standards, manufacturers must conduct several quality checks, such as:
- Tensile Strength Testing: Measures the force required to break the rubber, ensuring durability under stress.
- Hardness Testing: Confirms the part’s resistance to indentation and overall stiffness.
- Chemical Resistance Testing: Verifies that the rubber material can withstand exposure to oils, chemicals, or other harsh substances.
These tests ensure the part’s long-term reliability and compliance with safety standards, especially for applications where failure could be costly or dangerous.
5. Comparing Costs and Lead Times for Each Process
When deciding on a manufacturing method, companies often need to balance the costs and lead times associated with each option. Here’s a comparison to help you make an informed choice:
Process | Average Cost per Part | Lead Time | Suitable for |
---|---|---|---|
Injection Molding | High | Shorter | High-volume production |
Compression Molding | Lower | Medium | Low to medium volumes |
Transfer Molding | Moderate | Medium | Complex parts with medium volumes |
6. Addressing Common Challenges in Custom Rubber Part Manufacturing
Manufacturing custom rubber parts presents unique challenges, such as shrinkage, uneven vulcanization, and maintaining consistent tolerances. These issues can be mitigated by:
- Precise Temperature Control: Keeping mold temperatures consistent helps avoid warping and dimensional inconsistencies.
- Optimal Mold Design: Molds designed with shrinkage compensation ensure parts maintain their intended shape.
- Regular Maintenance: Regularly inspecting and cleaning molds helps reduce production errors and extend mold life.
Summary
Manufacturing custom rubber parts requires careful planning, from selecting the right material to choosing the optimal molding process. By understanding each step in the process, companies can achieve high-quality rubber parts that meet their exact specifications.
Contact our team of experts today to discuss your project needs and discover the best solution for your unique requirements.