Rubber manufacturing involves a complex process of mixing natural or synthetic rubber with additives, shaping it into desired forms, and curing it under heat and pressure to produce a wide range of products.
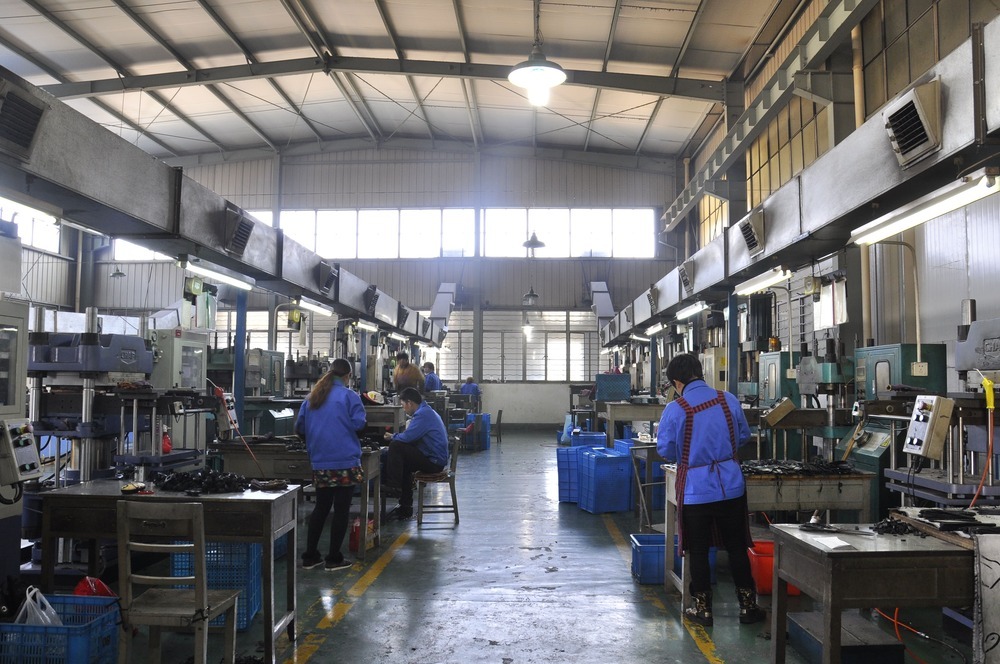
Introduction:
When it comes to the manufacturing of rubber products, there’s more than meets the eye. Whether you’re sourcing rubber seals, rubber hoses, or custom rubber molded parts, the production process and material selection can make or break your business.
In this article, we’ll discuss the key considerations in manufacturing high-quality rubber products for industrial applications, the various production methods, and how to ensure you’re making the right choices for your needs. Rubber product manufacturing is a multifaceted process that combines natural and synthetic materials, innovative techniques, and stringent quality controls to meet diverse industrial needs.
Key points:
- Material selection: Natural rubber vs. synthetic rubber.
- Production processes: Injection molding, extrusion, compression molding.
- Customization: Tailored designs for specific applications.
How to Choose the Right Rubber Material
Choosing the right rubber material is the first step to creating durable, reliable products. For example, rubber seals used in the automotive industry need to resist heat and chemicals, while rubber hoses for industrial machinery require flexibility and durability.
Here’s a quick breakdown of common rubber types used in industrial manufacturing:
Rubber Type | Best For | Key Features |
---|---|---|
NR (Natural Rubber) | Seals, Gaskets, Tires | High elasticity, excellent wear resistance |
NBR (Nitrile Rubber) | Automotive seals, hoses, gaskets | Excellent oil and chemical resistance |
EPDM (Ethylene Propylene Diene Monomer) | Outdoor seals, electrical components | Superior weather and ozone resistance |
SBR (Styrene-Butadiene Rubber) | Tires, rubber conveyor belts | Good abrasion resistance and wear properties |
Manufacturing Process for Rubber Products
The journey from raw materials to finished rubber products involves several key steps:
- Mixing: Rubber is combined with additives like fillers, pigments, and vulcanizing agents to achieve desired properties.
- Molding: The mixed rubber compound is shaped into the desired form using techniques like injection molding, compression molding, or extrusion.
- Injection Molding: Used for producing high-precision, complex parts like rubber seals and gaskets. The material is injected into a mold under high pressure, creating consistent parts in large quantities.
- Compression Molding: Great for producing large rubber parts in low-to-medium volumes. The rubber is placed in a mold cavity and compressed under heat and pressure to form the desired shape.
- Extrusion: This method is ideal for producing rubber hoses and profiles. The rubber compound is forced through a die to form continuous shapes, which are then cut to length.
- Curing: A process involving heat and pressure to cross-link the rubber molecules, resulting in a hardened and durable product.
- Finishing: The cured rubber products undergo finishing operations such as trimming, buffing, and inspection.
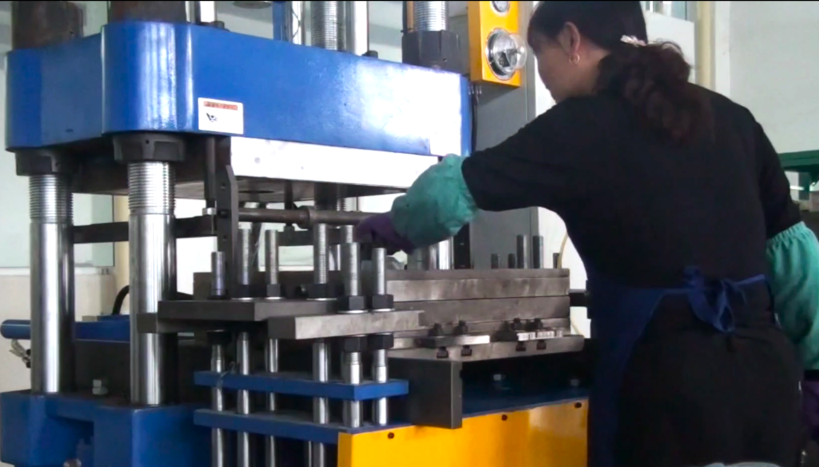
Rubber Product Performance: Factors That Matter
To create rubber products that truly perform, manufacturers must consider several key factors:
Aesthetics: The look and feel of the rubber product, especially in consumer-facing products.
Durability: Resistance to wear, tear, and environmental factors.
Elasticity: The ability to return to the original shape after compression or stretching.
Heat and Chemical Resistance: Ensuring the rubber can handle harsh industrial environments.
Common Issues in Rubber Product Manufacturing and How to Avoid Them
Even experienced manufacturers run into problems. Some common issues include:
- Inconsistent Material Quality: This can lead to product failure or a shorter lifespan.
- Molding Defects: Air bubbles or uneven curing can affect the part’s integrity.
- Overcomplicated Designs: Some custom designs may be too complex to manufacture cost-effectively.
To avoid these issues, it’s crucial to partner with a reputable supplier and make sure your designs are optimized for manufacturability.
How to Choose the Right Rubber Manufacturer for Your Needs
Choosing a manufacturer isn’t just about cost. You need to consider:
- Industry Experience: Look for a company with proven expertise in rubber products for your specific application.
- Customization Capability: Can they produce the custom rubber parts you need, such as specialized seals or molded components?
- Quality Control: Do they follow strict quality assurance processes to ensure consistency and reliability?
Frequently Asked Questions (FAQs)
Q1: What’s the difference between natural and synthetic rubber?
Natural rubber is derived from latex and offers excellent elasticity, while synthetic rubber is made through chemical processes and can be customized for specific industrial applications.
Q2: Can rubber products be used in extreme temperatures?
Yes, but the type of rubber used matters. Materials like EPDM and NBR are known for their high-temperature resistance.
Q3: How do I know if a rubber seal will work for my application?
Ensure the seal material is compatible with the chemicals, temperature, and pressure it will face. Consult with the manufacturer for recommendations based on your specific needs.
Conclusion: Investing in Quality Rubber Manufacturing
Manufacturing high-quality rubber products isn’t just about selecting the right materials—it’s about understanding the entire process from design to production. Whether you need custom rubber seals, rubber hoses, or automotive rubber components, the right approach to material selection, manufacturing process, and quality control will set you up for success.
Want to learn more? Reach out to our team today to discuss how we can provide custom rubber solutions tailored to your business needs. Let’s build something strong, reliable, and tailored to your business needs.