In the dynamic world of industrial components, the significance of bellows, especially rubber bellows, often goes unrecognized. These versatile components are integral in numerous industries, providing solutions that range from protection to facilitating movement and compensating for expansion.
Let’s explore their characteristics, suitable applications, and differences:
- Understanding the Vital Role of Bellows
- The Diversity of Bellows Types and Materials
- Applications Across Industries and the Role of Rubber Bellows
- Empowering Industries with the Right Bellows
Bellows are versatile components used across various industries, and they come in different types based on material, application, and purpose.
Material Matters: Rubber, Metal, and Plastic
Rubber Bellows: Known for their flexibility and durability, rubber bellows, made from either natural or synthetic rubber, are the go-to choice in the automotive and HVAC sectors. Their resistance to chemicals and temperature variations makes them highly versatile.
Rubber bellows are made from various types of rubber materials, each chosen for specific properties like elasticity, durability, chemical resistance, and temperature tolerance. Here's a comprehensive list of materials commonly used in the production of rubber bellows:
- Natural Rubber (NR):
- Known for good elasticity and tensile strength.
- Excellent abrasion resistance.
- Not suitable for applications involving oils and certain chemicals.
- Nitrile Rubber (NBR, Buna-N):
- Excellent resistance to oil and petroleum-based fluids.
- Good mechanical properties and wear resistance.
- Limited weathering resistance.
- Silicone Rubber (VMQ):
- Excellent high and low-temperature resistance.
- Good for applications requiring flexibility and durability in extreme conditions.
- Generally inert and resistant to many chemicals.
- Ethylene Propylene Diene Monomer (EPDM):
- Excellent resistance to weathering, ozone, and UV exposure.
- Good heat and chemical resistance.
- Not recommended for applications with petroleum oils and fuels.
- Chloroprene Rubber (Neoprene, CR):
- Good balance of weather, ozone, and chemical resistance.
- Flame retardant properties.
- Moderate resistance to oils.
- Fluoroelastomers (FKM, Viton®):
- Exceptional resistance to heat, oil, and chemicals.
- Suitable for high-temperature applications.
- Relatively expensive compared to other rubber types.
- Butyl Rubber (IIR):
- Excellent impermeability to gases and moisture.
- Good heat resistance.
- Limited resistance to petroleum fluids and sunlight.
- Styrene-Butadiene Rubber (SBR):
- Good abrasion resistance.
- Not recommended for applications involving ozone, strong acids, oils, greases, fats, and most hydrocarbons.
Each of these rubber types has unique properties making them suitable for different applications. The choice depends on factors like the environment in which the bellow will operate, exposure to chemicals, temperature ranges, and the required flexibility and durability. This variety allows rubber bellows to be widely used across numerous industries, from automotive to industrial machinery and beyond. However, they may fall short in high-heat scenarios where metal bellows excel.
Metal Bellows: The champions of high-temperature and pressure environments, metal bellows (crafted from stainless steel, brass, or copper) are indispensable in the aerospace and oil industries. Their robustness is unparalleled, though this comes at a higher cost and less flexibility compared to rubber or plastic.
Metal bellows are manufactured from a variety of metals and alloys, each selected for specific properties like strength, flexibility, temperature resistance, and corrosion resistance. Here's a comprehensive list of materials commonly used in the production of metal bellows:
- Stainless Steel:
- AISI 304
- AISI 316
- AISI 321
- AISI 316L
- AISI 347
- Nickel Alloys:
- Inconel 625
- Inconel 718
- Inconel X-750
- Monel 400
- Hastelloy C276
- Hastelloy C22
- High-Temperature Alloys:
- Incoloy 800
- Incoloy 825
- Copper Alloys:
- Phosphor bronze
- Beryllium copper
- Brass
- Titanium:
- Commercially pure titanium
- Titanium alloys
- Other Specialty Metals:
- Aluminum
- AM350 (a chromium-nickel-molybdenum alloy)
- Alloy 20 (a nickel-chromium-molybdenum stainless steel alloy)
Each of these materials offers unique advantages. For instance, stainless steels like AISI 321 are favored for their overall strength and corrosion resistance. Nickel alloys such as Inconel are chosen for applications involving extreme temperatures. Copper alloys are often used for their excellent thermal conductivity and flexibility. Titanium, known for its strength and lightweight properties, is suitable for high-performance applications.
Plastic Bellows: For less demanding environments, plastic bellows offer a lightweight, cost-effective solution. Made from materials like PVC and polyurethane, they are ideal for light machinery and electronic applications, providing adequate protection against corrosion but limited resistance to extreme conditions.
Plastic bellows are made from a variety of plastic materials, each selected for specific properties such as flexibility, chemical resistance, and durability. Here's a comprehensive list of materials commonly used in the production of plastic bellows:
- Polyvinyl Chloride (PVC):
- Good flexibility and chemical resistance.
- Widely used for its balance of toughness, cost, and versatility.
- Polyurethane (PU):
- Excellent abrasion resistance and flexibility.
- Good mechanical properties, including tear and impact resistance.
- Polyethylene (PE):
- Includes High-Density Polyethylene (HDPE) and Low-Density Polyethylene (LDPE).
- Good chemical resistance and low water absorption.
- HDPE offers higher strength and rigidity; LDPE is more flexible.
- Polypropylene (PP):
- Strong resistance to chemicals and solvents.
- High fatigue resistance.
- Suitable for applications requiring higher thermal resistance than PE.
- Thermoplastic Elastomers (TPE):
- Combines the properties of rubber with the processing advantages of thermoplastics.
- Good flexibility and stretchability.
- Often used where rubber-like flexibility is needed.
- Thermoplastic Polyolefin (TPO):
- Good impact resistance and durability.
- Resistant to UV light and many chemicals.
- Commonly used in automotive applications.
- Polycarbonate (PC):
- High impact resistance and excellent clarity.
- Good temperature resistance.
- Used in applications where transparency and toughness are required.
- Nylon (Polyamide, PA):
- High strength and stiffness.
- Good wear and chemical resistance.
- Suitable for mechanically demanding applications.
- Acetal (Polyoxymethylene, POM):
- High mechanical strength and rigidity.
- Low friction and good wear properties.
- Excellent dimensional stability.
- Fluoropolymers (e.g., PTFE, PVDF):
- Exceptional chemical and thermal resistance.
- PTFE is known for its non-stick properties.
- PVDF offers good chemical resistance and strength.
Each of these plastic materials offers unique advantages. The choice of material for plastic bellows depends on the specific requirements of the application, including factors like environmental exposure, required flexibility, and temperature ranges. This diversity allows plastic bellows to be utilized across a wide range of industries, including automotive, medical, and industrial sectors.
Protective vs. Expansion Bellows
Protective Bellows: These are designed to shield crucial machine parts from contaminants. Their adaptability to various shapes and environments makes them essential in safeguarding machinery and automotive components.
Expansion Bellows: Engineered to absorb thermal expansion in piping systems, these bellows stand up to high pressure and temperature changes, making them vital in industrial and HVAC applications.
Protective Bellows and Expansion Bellows, while similar in their fundamental purpose of providing protection and flexibility, are typically made from different materials due to their distinct applications. Here's a breakdown of their usual materials and key differences:
Protective Bellows
- Common Materials:
- Rubber: Often used due to its flexibility and durability. Rubber is ideal for applications requiring adaptability to various shapes and resistance to environmental factors like water, dust, and certain chemicals.
- Plastic: Used in less demanding environments, plastic bellows are lightweight and cost-effective. Materials like PVC and polyurethane are common.
- Fabric: In some cases, coated fabrics are used for protective bellows, especially when there is a need for a very flexible, lightweight material.
- Key Characteristics:
- Designed to protect parts like screws, rods, and shafts from dust, moisture, and other contaminants.
- Generally more flexible to accommodate a range of movements.
- Less focused on tolerating extreme temperature and pressure compared to expansion bellows.
Expansion Bellows
- Common Materials:
- Metal: Stainless steel and other alloys are commonly used for expansion bellows. They are chosen for their ability to withstand high temperatures and pressures.
- Rubber and Elastomers: In systems where less extreme conditions prevail, rubber or synthetic elastomers can be used. These materials provide good flexibility and are capable of handling moderate temperature and pressure changes.
- Key Characteristics:
- Specifically designed to absorb and compensate for thermal expansion and contraction in piping systems and ducts.
- Must withstand significant changes in temperature and pressure.
- Often more robust in construction compared to protective bellows, especially metal expansion bellows.
Distinct Differences
- Material Suitability: Protective bellows often use more flexible materials like rubber and fabric, whereas expansion bellows frequently require the strength and resilience of metals.
- Environmental Tolerance: Expansion bellows need to handle more extreme environmental conditions, especially in industrial settings, compared to protective bellows.
- Design Focus: Protective bellows focus on shielding components from environmental factors and contaminants, while expansion bellows are designed to deal with physical changes in system dimensions due to thermal variations.
- Structure: Rubber expansion bellows are usually composed of an inner tube, an outer tube, and bellows. The inner tube and outer tube can be made of metal pipes or plastic pipes, and the bellows are made of rubber. Rubber bellows are usually made of single-layer or multi-layer rubber.
- Function: The main function of rubber expansion bellows is to absorb the displacement caused by thermal expansion and contraction, vibration, etc. in pipe systems, while the main function of rubber bellows is to connect pipes and play a role in sealing and vibration reduction.
- Application range: Rubber expansion bellows are widely used in pipelines, equipment, and containers, while rubber bellows are mainly used in pipe connection, sealing, and vibration reduction.
Here are some examples of the applications of rubber expansion bellows and rubber protective bellows:
- Rubber expansion bellows:
- Used in the pipe systems of factories such as thermal power plants and chemical plants to absorb the displacement caused by thermal expansion and contraction of the pipe systems.
- Used in the pipe systems of buildings to absorb the displacement caused by earthquakes and other factors in the pipe systems.
- Used in the pipe systems of vehicles such as ships and airplanes to absorb the displacement caused by vibration in the pipe systems.
- Rubber protective bellows:
- Used to connect pipes and play a role in sealing and vibration reduction.
- Used in liquid or gas conveying pipe systems to play a role in sealing and vibration reduction.
- Used in pipe systems of equipment such as automobiles and machinery to play a role in sealing and vibration reduction.
In summary, the choice between rubber, plastic, fabric, or metal in bellows depends on their specific application, with protective bellows leaning towards materials that offer flexibility and environmental resistance, and expansion bellows requiring materials that can endure high temperatures and pressures.
Applications Across Industries
Automotive Excellence: In the automotive realm, bellows are crucial for protecting systems and ensuring smooth operation. They must withstand automotive fluids and varying temperatures, reflecting the stringent standards of the industry.
Industrial Giants: In the industrial sector, bellows are larger and more robust, catering to a range of machinery and manufacturing equipment. Their durability and material versatility are key to their performance.
Aerospace Pioneers: Aerospace bellows are a class apart. Meeting the extreme demands of aircraft and spacecraft, they offer exceptional resistance to temperature and pressure, highlighting the advancement in material science.
From automotive to aerospace, rubber bellows are a versatile solution that effectively tackles dynamic sealing challenges across various industries. These flexible components play a vital role in ensuring the integrity and efficiency of complex systems, providing crucial protection against dust, dirt, vibrations, and other environmental factors.
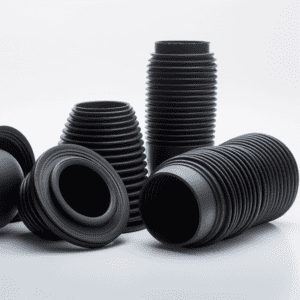
In the automotive sector, rubber bellows act as a barrier, sealing critical components such as steering systems, suspension parts, and air intake systems. They enable smooth and reliable operation while safeguarding against contaminants, contributing to enhanced performance and longevity of vehicles.
In the aerospace industry, rubber bellows are equally indispensable. They are utilized in systems such as aircraft engines, pumps, and landing gear to prevent fluid and gas leakage, withstand high-pressure conditions, and absorb vibrations caused by intense operational demands.
With their ability to withstand extreme temperatures, corrosive substances, and challenging working conditions, rubber bellows provide a dependable sealing solution that meets the rigorous requirements of diverse sectors.
Whether it's maintaining precision in automotive mechanisms or ensuring safety in aerospace systems, rubber bellows offer a reliable and efficient solution that keeps industries moving forward.
We will bring more details on topics as follows:
- The importance of dynamic sealing in the automotive industry
- Rubber bellows applications in the automotive sector
- Dynamic sealing challenges in the aerospace industry
- Dynamic sealing in the medical sector and the role of rubber bellows
- And Much More…
The importance of dynamic sealing in the automotive industry
In the automotive sector, dynamic sealing is of utmost importance to ensure the smooth operation and longevity of vehicles. Rubber bellows act as a barrier, sealing critical components such as steering systems, suspension parts, and air intake systems. These components prevent the ingress of contaminants, ensuring efficient performance and minimizing the risk of damage or malfunction.
Rubber bellows are specifically designed to withstand the demanding conditions experienced in automotive applications. They are engineered to resist extreme temperatures, corrosive substances, and mechanical stress, ensuring reliable sealing even in the harshest environments.
By effectively sealing critical components, rubber bellows contribute to the overall safety and performance of vehicles, allowing for a smooth and comfortable driving experience.
In addition to their sealing capabilities, rubber bellows also play a crucial role in absorbing vibrations and reducing noise. The flexible nature of these components allows them to dampen vibrations caused by engine operation, road conditions, or other external factors.
This not only enhances the comfort of the driver and passengers but also protects other components from excessive wear and tear.
Rubber bellows applications in the automotive sector
Rubber bellows find extensive applications in various automotive systems.
One of the key areas where these components are utilized is in steering systems.
The steering bellows, also known as steering rack boots, provide a protective cover for the steering rack and pinion, preventing the ingress of dirt, debris, and moisture.
This ensures the smooth and reliable functioning of the steering system, eliminating the risk of premature failure and ensuring precise and responsive steering control.
Another important application of rubber bellows in the automotive sector is in suspension systems.
Suspension bellows are used to seal the joints and connections in suspension components such as shock absorbers and struts. These bellows protect the internal components from dirt, moisture, and other contaminants, preventing premature wear and maintaining the optimal performance of the suspension system.
Rubber bellows are also employed in air intake systems in vehicles.
Air intake bellows, commonly known as air intake hoses, provide a sealed connection between the air filter box and the engine intake manifold. These bellows ensure that only clean, filtered air enters the engine, preventing the entry of dust, dirt, and other contaminants. By maintaining the cleanliness of the intake air, rubber bellows contribute to the efficient combustion process, optimizing engine performance and fuel economy.
Dynamic sealing challenges in the aerospace industry
While dynamic sealing is essential in the automotive sector, its significance is equally vital in the aerospace industry. Aerospace systems operate in extreme conditions, including high temperatures, high pressures, and intense vibrations. The sealing solutions employed in these applications must be capable of withstanding these demanding environments while ensuring the integrity and safety of the systems.
One of the major challenges in aerospace dynamic sealing is the prevention of fluid and gas leakage. Aerospace systems, such as aircraft engines, pumps, and landing gear, rely on effective sealing to maintain the required fluid pressure and prevent leaks that could compromise the system's performance or safety. Rubber bellows offer a reliable solution to these challenges, as they can provide an airtight and watertight seal even in high-pressure conditions.
Another significant challenge in aerospace dynamic sealing is the absorption of vibrations. Aerospace systems experience intense vibrations during operation, which can lead to excessive wear and potential damage to critical components. Rubber bellows excel in absorbing these vibrations, acting as a cushion and reducing the impact on the system. By dampening vibrations, rubber bellows contribute to the overall safety and reliability of aerospace systems.
Rubber bellows solutions for aerospace applications
Rubber bellows find wide-ranging applications in the aerospace industry, addressing the dynamic sealing challenges faced by various systems. In aircraft engines, for example, rubber bellows are used to seal the joints and connections in fuel systems, lubrication systems, and ventilation systems.
These bellows ensure the proper flow of fluids while preventing leakage and maintaining the required pressure levels.
In addition to engine applications, rubber bellows are also utilized in aerospace pumps.
Pump bellows provide a reliable seal between the rotating and stationary parts of the pump, preventing the leakage of fluids and gases. These bellows are designed to withstand high-pressure conditions and maintain their sealing capabilities even when subjected to extreme temperatures and vibrations.
Rubber bellows are also crucial in aerospace landing gear systems. Landing gear bellows protect the hydraulic cylinders and other critical components from environmental factors such as dust, dirt, and moisture. These bellows ensure effective sealing while absorbing the vibrations and shocks experienced during takeoff, landing, and taxiing. By providing reliable sealing and vibration dampening, rubber bellows contribute to the safe and efficient operation of landing gear systems.
Dynamic sealing in the medical sector and the role of rubber bellows
Dynamic sealing is not limited to the automotive and aerospace sectors. The medical industry also relies on effective sealing solutions to ensure the integrity and reliability of various medical devices and equipment. Rubber bellows play a crucial role in sealing medical systems, providing protection against contaminants, and maintaining the required performance standards.
In medical equipment such as infusion pumps, rubber bellows are utilized to seal the fluid pathways, preventing leakage and ensuring accurate and controlled delivery of medications or fluids. These bellows are designed to meet stringent regulatory requirements and are made from materials that are compatible with medical-grade substances.
Rubber bellows are also employed in diagnostic equipment such as ultrasound machines and endoscopes. These bellows seal the sensitive components, protecting them from dust, dirt, and moisture. By maintaining a clean and controlled environment, rubber bellows contribute to accurate and reliable diagnostic results.
Rubber bellows in industrial machinery and equipment
Beyond the automotive, aerospace, and medical sectors, rubber bellows find applications in various industrial machinery and equipment. Dynamic sealing is essential in industrial settings where machines and equipment operate under demanding conditions, often exposed to contaminants, vibrations, and extreme temperatures.
In industrial pumps and compressors, rubber bellows are used to seal the rotating shafts, preventing the leakage of fluids or gases. These bellows are designed to withstand high pressures and provide reliable sealing even in harsh environments. By effectively sealing the shafts, rubber bellows contribute to the efficiency and longevity of these machines.
Rubber bellows also play a vital role in industrial valves. Valve bellows provide a flexible and durable sealing solution for the moving parts of valves, ensuring a tight seal and preventing leakage. These bellows are designed to withstand the corrosive substances often encountered in industrial processes, offering long-lasting and reliable sealing performance.
Other sectors that benefit from rubber bellows for dynamic sealing
Industrial Applications:
In industrial settings, rubber bellows are critical components in machinery and conveyor systems. They serve as flexible connectors and protective covers for moving parts, effectively preventing the ingress of dust, debris, and industrial contaminants. This protection is essential to maintain machinery efficiency and prevent premature wear or failure, particularly in high-particulate environments such as manufacturing plants and processing facilities.
HVAC Systems:
Within HVAC systems, rubber bellows play a vital role in reducing vibration and noise transmission from equipment like compressors, blowers, and fans. They provide a flexible connection between ductwork components, accommodating thermal expansion and movement, which is crucial for maintaining system integrity and efficiency. By isolating vibrations and allowing for movement, these bellows help extend the life of the HVAC system while ensuring smooth and quiet operation.
Water and Wastewater Management:
In water and wastewater management, rubber bellows are employed in pipelines and pumping systems to absorb movement and vibration. They act as critical components in mitigating the stress on pipes and fittings caused by water hammer, pump operations, and thermal expansion. This functionality is crucial in preventing leaks and ruptures in water treatment plants, distribution systems, and wastewater facilities, thereby ensuring continuous, uninterrupted service.
Building Services:
In the realm of building services, rubber bellows find extensive use in plumbing systems to accommodate pipe movement and alignment. They serve as expansion joints in water supply and drainage systems, absorbing vibrations and noise from building movements and water flow. Their ability to flex and adapt to structural shifts ensures the longevity and integrity of the plumbing infrastructure within commercial and residential buildings, safeguarding against potential damages and leaks.
Marine Sector
In the marine sector, rubber bellows are utilized in marine engines, water pumps, and cooling systems to provide effective sealing and withstand the challenging conditions encountered at sea. These bellows prevent the entry of water, sand, and other contaminants, protecting the internal components from damage and corrosion.
Construction Industry
In the construction industry, rubber bellows find applications in construction machinery such as excavators, loaders, and cranes. These bellows seal the moving parts, protecting them from dust, dirt, and debris. By maintaining a clean and sealed environment, rubber bellows contribute to the reliability and performance of construction equipment.
Energy Sector
Rubber bellows are also employed in the energy sector, particularly in power plants and renewable energy systems. From gas turbines to wind turbines, these bellows provide sealing solutions that can withstand high temperatures, vibrations, and other challenging conditions. By effectively sealing critical components, rubber bellows contribute to the efficiency and reliability of energy generation systems.
Choosing the right rubber bellows for your industry
When selecting rubber bellows for dynamic sealing applications, it is crucial to consider the specific requirements and operating conditions of your industry. Factors such as temperature range, chemical compatibility, pressure resistance, and expected lifespan should be taken into consideration.
Consulting with experienced rubber bellows manufacturers or suppliers is recommended to ensure the selection of the most suitable bellows for your industry. These experts can guide material selection, design considerations, and customization options to meet your specific needs.
Are you looking to elevate your industrial components with the right type of rubber bellows? Connect with us for expert advice and a range of high-quality rubber bellows tailored to your industry needs. Our expertise in providing cutting-edge solutions will ensure your machinery's peak performance and longevity.
Contact us today to explore our range and find the perfect bellow solution for your industry!