Introduction
Rubber hole plugs are simple yet indispensable tools used to seal, protect, and cover openings in various applications. Made from, you guessed it, rubber, they come in a variety of sizes, shapes, and material compositions to fit diverse needs.
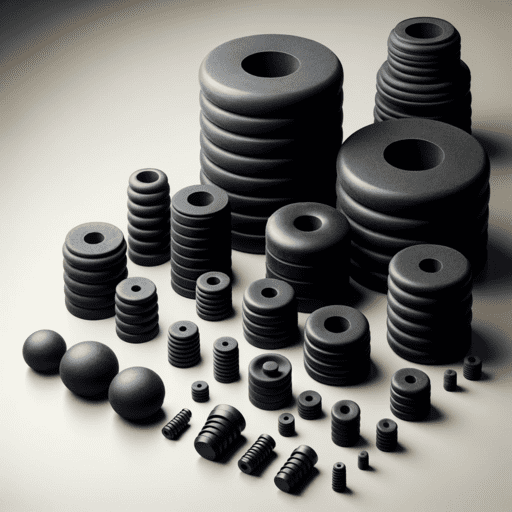
Here's a breakdown of their key features:
Function:
- Sealing: They create a watertight and airtight barrier, preventing leaks, spills, and entry of dust, debris, and contaminants.
- Protecting: They shield sensitive components and internal workings from external elements that could damage them.
- Covering: They offer a neat and aesthetically pleasing way to mask unused openings or access points.
Benefits:
- Versatility: Used across industries, from machinery and electrical systems to automotive and furniture.
- Durability: Crafted from resilient rubber compounds to withstand wear, tear, and environmental factors.
- Cost-effectiveness: An affordable solution compared to more complex sealing methods.
- Ease of use: Often designed for simple installation and removal.
Types:
- Compression plugs: Expand by pushing them into the hole, ideal for general applications.
- Expansion plugs: Contract inside the hole for a secure fit, perfect for irregular openings.
- Flange plugs: Feature a wide rim for anchoring in place, suitable for exposed areas.
Key Applications of Rubber Hole Plugs:
Rubber hole plugs offer a simple yet powerful solution for various needs across diverse industries. Here's a glimpse into some of their key applications:
Industrial Machinery:
- Sealing unused ports and valves on equipment to prevent dust, debris, and moisture ingress.
- Protecting electrical connections and sensitive components from environmental factors.
- Plugging temporary access points during maintenance or repairs.
Automotive Industry:
- Masking unused screw holes and gaps in car interiors and exteriors.
- Plugging temporary openings left during fabrication or repairs.
- Protecting electrical components from water and dust under the hood.
Electrical Work:
- Blocking unused electrical outlets and conduit openings to ensure safety and prevent dust accumulation.
- Protecting unused cable connections from moisture and corrosion.
- Sealing temporary wiring access points during electrical installations.
Construction and Building:
- Plugging unused pipe and plumbing connections during construction or before fixture installation.
- Covering temporary access points and holes in walls and ceilings for painting or finishing work.
- Protecting exposed electrical connections from dust and debris during construction.
Marine and Watercraft:
- Sealing unused deck fittings and access points to prevent water ingress.
- Plugging temporary drain holes for maintenance or repairs.
- Protecting sensitive electrical components from salt spray and moisture.
Furniture and Woodworking:
- Masking screw holes and imperfections on furniture surfaces for a clean and finished look.
- Plugging unused bolt holes in wood panels and beams.
- Protecting internal compartments from dust and debris.
This list is just a starting point, and the applications for rubber hole plugs extend far beyond these examples. Their versatility, durability, and cost-effectiveness make them a valuable tool for professionals and DIY enthusiasts across numerous industries.
Remember, the specific application will determine the ideal material, size, and shape of the rubber hole plug. By choosing the right plug for the job and following proper installation practices, you can ensure optimal performance and longevity.
How to Choose the Right Rubber Hole Plug
Here's a guide to choosing the right rubber hole plug for your specific needs:
1. Material:
- Neoprene: General-purpose, good for water and oil resistance, moderate chemical resistance.
- Nitrile: Excellent oil and fuel resistance, good for high temperatures.
- EPDM: Excellent weather resistance, ozone and UV resistant, good for outdoor applications.
- Silicone: Wide temperature range, good chemical resistance, food-grade options available.
- Fluoropolymers: Outstanding chemical resistance, high-temperature resistance, limited flexibility.
2. Size:
- Measure the hole diameter accurately.
- Choose a plug with a slightly larger diameter for compression plugs to ensure a tight fit.
- Choose a plug with the exact diameter for expansion plugs.
3. Shape:
- Round: Most common, suitable for general applications.
- Square or rectangular: For specific spaces or surface alignment.
- Tapered: For tapered holes or easier insertion.
- Flanged: For added grip and security, especially in exposed areas.
4. Application Requirements:
- Temperature: Consider the minimum and maximum temperatures the plug will be exposed to.
- Chemical exposure: Choose a material compatible with the chemicals present.
- Pressure: Ensure the plug can withstand the expected pressure.
- Accessibility: Choose a plug that's easy to install and remove if needed.
- Aesthetics: Consider the plug's appearance if it is visible.
Additional Considerations:
- Color: Available in various colors for visual identification or aesthetics.
- Finish: Smooth or textured finishes for different applications.
- Installation method: Push-in, threaded, or adhesive-backed options.
Recommendations:
- Consult with a supplier or manufacturer for expert advice if you have specific or complex requirements.
- Request material safety data sheets (MSDS) for detailed information on chemical compatibility and safety precautions.
- Inspect plugs regularly for wear and tear, especially in harsh environments or critical applications.
By carefully considering these factors, you can select the ideal rubber hole plug that effectively seals, protects, and meets the demands of your particular application.
Best Practices in Installation for Rubber Hole Plugs:
Rubber hole plugs offer a simple yet effective way to seal, protect, and cover openings. However, proper installation is crucial for ensuring their functionality and longevity. Here are some best practices to follow:
Preparation:
- Clean the surface: Thoroughly clean the hole and surrounding area with a mild detergent or solvent to remove dirt, grease, and debris. This ensures a good seal and prevents the plug from slipping out.
- Dry the surface: Ensure the hole and surrounding area are completely dry before installation. Moisture can compromise the seal and lead to leaks.
- Inspect the plug: Check the plug for any damage or imperfections that could affect its performance.
Installation:
- Choose the right size: Select a plug with the appropriate diameter for the hole. For compression plugs, choose one slightly larger than the hole for a secure fit. For expansion plugs, choose one with the exact diameter.
- Select the right installation method: Different types of plugs have different installation methods. Follow the manufacturer's instructions for your specific plug type. Common methods include pushing, screwing, or using an adhesive.
- Apply force evenly: When installing a compression plug, apply force evenly around the circumference to ensure a tight seal. For expansion plugs, insert the plug completely and allow it to expand to fill the hole.
- Use the right tools: If necessary, use appropriate tools like pliers or screwdrivers for a secure and controlled installation.
Additional Tips:
- Lubricate the plug (optional): Applying a light lubricant, like silicone grease, can help the plug slide into the hole more easily and prevent tearing.
- Test the seal: After installation, check for leaks or gaps by pouring water or blowing air around the plug.
- Monitor and maintain: Regularly inspect the plug for signs of wear and tear, especially in harsh environments. Replace it promptly if necessary.
By following these best practices, you can ensure that your rubber hole plugs are installed correctly and perform effectively for their intended purpose.
Tip: Consider using a plug with a flange for extra security, especially in applications where the plug may be exposed to external forces or pressure.
Remember, proper installation is key to maximizing the benefits of rubber hole plugs. By taking the time to prepare, choose the right plug and installation method, and follow these best practices, you can ensure their long-lasting performance and optimal protection for your applications.
Conclusion
Rubber hole plugs are a versatile and effective way to seal, protect, and cover openings in a wide range of applications. By following the best practices outlined in this guide, you can ensure that your rubber hole plugs are installed correctly and perform effectively for their intended purpose.
We offer a wide variety of rubber hole plugs in a variety of materials and sizes to suit your specific needs. We can help you choose the right plug for your application and ensure that it is installed correctly.
Contact Julong Rubber today to learn more about our rubber hole plugs and how they can benefit your business.