Rubber stoppers, also known as rubber bungs or corks, are versatile components widely used across various industries, including pharmaceuticals, laboratories, food and beverage, and manufacturing. Their primary function is to seal containers, preventing contamination and ensuring the integrity of the contents. This article explores the different types of rubber stoppers, their applications, and the benefits they offer in industrial settings.
What is a Rubber Stoppers
A rubber stopper is a small, tapered plug designed to seal the openings of containers such as test tubes, flasks, and other laboratory glassware. These stoppers are typically made from rubber or other flexible materials and are preferred over cork stoppers for applications requiring a tighter seal and better chemical resistance.
Rubber stoppers are made from various types of rubber, including natural rubber and synthetic options like neoprene, Viton, and urethane. Each type of rubber offers unique properties that make it suitable for specific applications.
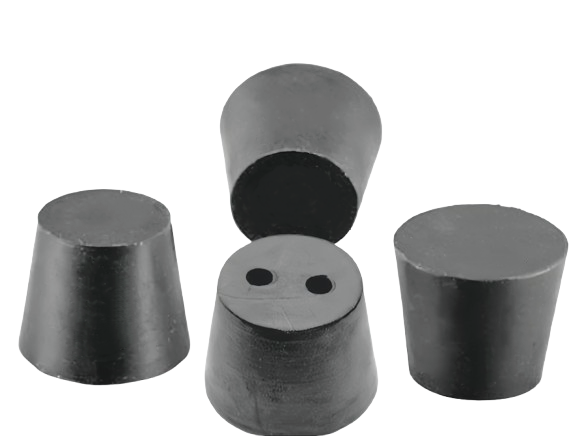
Purpose of Rubber Stoppers
The primary functions of rubber stoppers include:
- Sealing: They prevent gases or liquids from escaping during experiments, ensuring that the contents remain contained.
- Contamination Prevention: Rubber stoppers protect samples from air exposure, reducing the risk of oxidation and contamination.
- Facilitating Mixing: They allow for shaking or mixing of solutions without spillage, maintaining the integrity of the experiment.
Characteristics
Rubber stoppers are characterized by:
- Shape: Typically cylindrical with a tapered bottom for easy insertion.
- Size: Available in various sizes, ranging from small (0.5 inches) to larger sizes (up to 5 inches) to fit different types of glassware.
- Properties: They exhibit elasticity, chemical resistance, and impermeability, making them suitable for various laboratory conditions.
Key Properties of Rubber Stoppers:
- Elasticity: Allows for a tight seal when inserted into openings.
- Chemical Resistance: Many rubber stoppers are resistant to a wide range of chemicals.
- Temperature Tolerance: Capable of withstanding extreme temperatures without losing integrity.
- Impermeability: Prevents the escape of gases and liquids.
Types of Rubber Stoppers
Rubber stoppers come in various designs to suit different needs:
- Solid Rubber Stoppers
- Used for sealing bottles and containers in home brewing and laboratory settings.
- One-Hole Rubber Stoppers
- Commonly used in laboratories for test tubes and flasks.
- Allows for the insertion of a single tube or probe while maintaining a seal.
- Two-Hole Rubber Stoppers
- Suitable for laboratory applications where multiple tubes need to be inserted.
- Ideal for experiments requiring gas exchange or liquid transfer.
- Three-Hole Rubber Stoppers
- Designed for complex laboratory setups involving multiple connections.
- Frequently used in chemical reactions where several gases or liquids need to be managed.
- Self-Sealing Rubber Stoppers
- Feature a valve or slit that allows syringes or needles to be inserted while maintaining an airtight seal.
- Commonly used in medical applications.
- Tapered Rubber Stoppers:
- These stoppers have a cone-shaped design that allows them to fit into various-sized openings, providing a tight seal in lab glassware or other containers.
- Lyophilisation Stoppers:
- Specifically designed for the freeze-drying process in pharmaceuticals, these stoppers can withstand extreme temperatures and vacuum conditions.
- Specialized Rubber Stoppers:
- These include high-temperature-resistant and chemical-resistant stoppers tailored for specific industrial applications.
- Push-Fit Caps:
- These caps provide a tight fit without the need for fasteners and are often used for storage and transportation purposes.
Each type of rubber stopper serves unique functions across various industries, including laboratory work, pharmaceuticals, food and beverage production, and manufacturing processes. The choice of stopper depends on factors such as the application, container size and shape, sealing requirements, and any specialized needs related to temperature or chemical exposure.
Applications of Rubber Stoppers
Rubber stoppers are integral to various industries due to their sealing capabilities:
- Laboratories: Essential for sealing test tubes, flasks, and other glassware to prevent contamination and maintain controlled environments during experiments.
- Pharmaceuticals: Used in vials and syringes to protect medications from contamination and ensure sterility.
- Food and Beverage: Commonly found in wine and beer production to seal fermentation vessels, preserving flavor and preventing spoilage.
- Industrial Uses: Employed in manufacturing processes where sealing is critical to prevent leaks and maintain product quality.
Comparative Analysis of Rubber Stopper Materials
When selecting rubber stoppers for specific applications, consider the material properties:
Material Type | Temperature Range | Chemical Resistance | Common Uses |
---|---|---|---|
Natural Rubber | -40°F to +160°F | Moderate | General sealing |
Neoprene | -65°F to +250°F | Good | Outdoor applications |
Viton | -20°F to +400°F | Excellent | Chemical processing |
Silicone | -80°F to +550°F | Excellent | Food processing |
Benefits of Using Rubber Stoppers
Rubber stoppers offer numerous advantages:
- Durability: Long-lasting materials reduce the need for frequent replacements.
- Versatility: Suitable for a wide range of applications across multiple industries.
- Cost-Effectiveness: Reliable sealing solutions can lead to reduced waste and improved efficiency.
Conclusion
Rubber stoppers are essential components that provide effective sealing solutions across various sectors. Understanding the different types available and their specific applications can help businesses select the right product for their needs. By ensuring proper sealing with high-quality rubber stoppers, companies can enhance safety, maintain product integrity, and improve operational efficiency. For tailored solutions or inquiries about our range of rubber stoppers designed for your specific applications, please contact us today. Let our experts assist you in finding the perfect sealing solution that meets your operational demands!