Materials of Excellence
Crafting with the Best in the Business
At Julong Rubber, we prioritize using the finest materials to ensure the durability, efficiency, and performance of every product. Explore the various high-quality materials that form the foundation of our premium rubber components.
Styrene-Butadiene Rubber (SBR)
Styrene-Butadiene Rubber (SBR) is one of the most widely used synthetic rubbers in the world. But how does it compare to other rubber types, and what makes it so popular in industrial and commercial applications?
SBR is a synthetic rubber made from styrene and butadiene. It offers excellent abrasion resistance, good aging stability, and cost-effectiveness, making it a preferred material in tires, seals, and industrial rubber products.
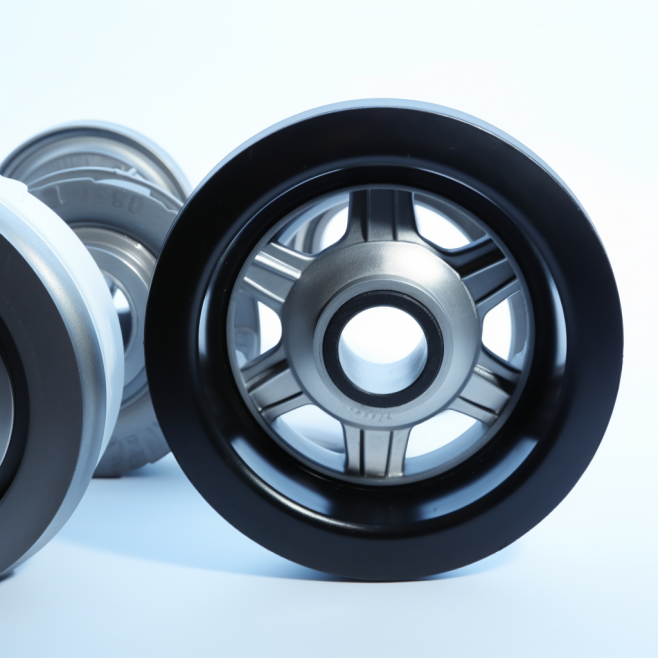
What is SBR (Styrene-Butadiene) Rubber?
Styrene-Butadiene Rubber (SBR) is a synthetic rubber derived from styrene and butadiene through a polymerization process. It was initially developed as a substitute for natural rubber.
SBR is a durable and versatile synthetic rubber known for its excellent abrasion resistance, flexibility, and affordability. It is commonly used in tires, footwear, seals, and industrial applications.
Chemical Structure and Types of SBR
The ratio of styrene to butadiene in SBR impacts its performance:
- More Styrene: Increases hardness and strength.
- More Butadiene: Enhances flexibility and elasticity.
Two main types of SBR exist:
- Emulsion-SBR (E-SBR): Common in tires and industrial applications.
- Solution-SBR (S-SBR): Offers improved rolling resistance and wet traction, ideal for high-performance tires.
Key Properties of SBR:
- ✅ High abrasion resistance
- ✅ Good aging stability
- ✅ Cost-effective compared to natural rubber
- ✅ Moderate flexibility and elasticity
- ✅ Resistant to mild chemicals and heat
Who Makes SBR Rubber?
Many global manufacturers produce SBR rubber, supplying industries worldwide. Some of the largest producers include:
- Goodyear Chemical (USA)
- Trinseo (Global)
- Synthos (Europe)
- Arlanxeo (Germany)
- Kumho Petrochemical (South Korea)
- LG Chem (South Korea)
What are the Pros and Cons of SBR Rubber?
Advantages of SBR Rubber
Advantage | Description |
---|---|
High Abrasion Resistance | Ideal for tires, conveyor belts, and footwear soles |
Good Aging Stability | Resists wear and maintains shape over time |
Affordable | Lower cost compared to natural rubber and other synthetics |
Moderate Flexibility | Can be formulated for different flexibility levels |
Water Resistance | Offers good water resistance but not fully waterproof |
Disadvantages of SBR Rubber
Disadvantage | Description |
---|---|
Lower Elasticity than Natural Rubber | Does not stretch as much as latex-based rubbers |
Limited Chemical Resistance | Not ideal for exposure to strong solvents or oils |
Not as Weather-Resistant as EPDM | UV and ozone exposure can degrade SBR over time |
What is Styrene-Butadiene Rubber (SBR) Used For?
SBR is commonly used in tires, conveyor belts, seals, and shoe soles due to its abrasion resistance and affordability.
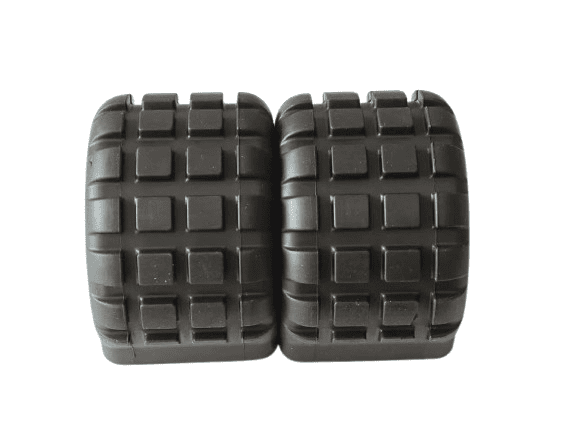
Major Applications of SBR
- Automotive Industry: Tires, seals, brake pads
- Industrial Applications: Conveyor belts, hoses, rubber flooring
- Footwear & Consumer Goods: Shoe soles, rubber mats, shock-absorbing pads
Is SBR Rubber Better Than Neoprene?
SBR is more affordable and abrasion-resistant, while neoprene provides better weather, chemical, and oil resistance.
SBR vs. Neoprene: Key Differences
Feature | SBR ✅ | Neoprene ✅ |
---|---|---|
Abrasion Resistance | High | Moderate |
Weather & UV Resistance | Moderate | High |
Chemical Resistance | Low | High |
Water Resistance | Good | Excellent |
Cost | Lower | Higher |
How Long Does SBR Rubber Last?
The durability of SBR depends on the environment and use. Indoors, SBR products can last 10-15 years. Outdoor exposure to UV and ozone reduces lifespan to about 5-10 years without protective treatments.
Condition | Expected Lifespan |
---|---|
Indoor Use | 10-15 years |
Outdoor Use (UV Exposure) | 5-10 years |
Heavy Industrial Use | 3-7 years |
Commonly Asked Questions About SBR Rubber
Can SBR Be Recycled?
Yes, SBR is recyclable. It is often used in recycled rubber applications such as playground flooring and reprocessed tires.
Is SBR Safe for Potable Water Applications?
No, SBR is not certified for drinking water contact. Materials like EPDM or silicone are better suited for such applications.
Is SBR Fire Resistant?
No, SBR is not inherently flame-retardant. Flame-retardant additives are needed for applications requiring fire resistance.
Does SBR Contain Latex?
No, SBR does not contain natural latex, making it a safer choice for those with latex allergies.
Is SBR rubber flexible?
Yes, SBR rubber is moderately flexible but not as stretchable as natural rubber or silicone.
Is SBR rubber waterproof?
SBR is water-resistant but not fully waterproof. For full waterproofing, EPDM or neoprene is better suited.
Does SBR stick to plastic?
SBR does not naturally adhere to plastic without adhesives or primers.
Is SBR rubber toxic to humans?
SBR is generally safe for humans but not suitable for food or medical-grade applications due to potential residual styrene content.
Conclusion
Styrene-Butadiene Rubber (SBR) is a cost-effective, abrasion-resistant synthetic rubber used in tires, industrial applications, and consumer goods. While it lacks chemical and weather resistance compared to neoprene and EPDM, it remains a reliable material for many applications.
🔗 Explore Other Rubber Materials
Custom Rubber Parts with Easy
At Julong Rubber, We turn complex Into Simple! Follow the following 3 steps to start today!

Tell Us What You Need
Tell us as specific as possible of your needs, provide the drawing, reference picture and share your idea.
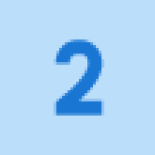
Get Solution & Quote
We will work on the best solution according to your requirements and drawing, the specific quote will be provided within 24 hours.

Approve for Mass Production
We will start mass production after getting your approval and deposit, and we will handle the shipment.
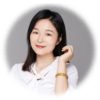
Get A Free Quote
Contact us to get a free quote and more expertise about custom rubber parts. Your project will meet the right solution at Julong Rubber.
Email:info@rubberandseal.com