Materials of Excellence
Crafting with the Best in the Business
At Julong Rubber, we prioritize using the finest materials to ensure the durability, efficiency, and performance of every product. Explore the various high-quality materials that form the foundation of our premium rubber components.

Silicone Rubber (VMQ)
The High-Temperature Champion
Silicone Rubber is renowned for its ability to retain flexibility and structural integrity in extreme temperature conditions, both high and low. Additionally, it resists degradation from UV light and ozone. These traits, combined with its inertness, make it especially valuable in both industrial and consumer applications.
Silicone Rubber (VMQ): Properties, Applications
Silicone rubber (VMQ) is widely recognized for its excellent flexibility, thermal stability, and safety in both industrial and consumer applications. Whether you are choosing materials for food-grade seals or high-temperature gaskets, understanding VMQ silicone’s properties is critical.
VMQ silicone rubber is a versatile elastomer known for its excellent heat resistance, flexibility, and biocompatibility. It is commonly used in medical, food, automotive, and electronic industries for seals, gaskets, tubing, and more.
What is VMQ Silicone?
VMQ stands for Vinyl Methyl Silicone, a type of silicone rubber primarily made from polydimethylsiloxane (PDMS) with vinyl groups added to improve its properties. It is categorized under silicone elastomers with excellent resistance to high and low temperatures, ranging from -60°C to +200°C (and even higher with special grades).
VMQ silicone rubber is a high-performance elastomer used for its flexibility, heat resistance, and electrical insulating properties in a wide range of industries.
Types of Silicone Rubber
Silicone rubber comes in several types, each designed for specific applications and environments:
- VMQ (Methyl Vinyl Silicone) – General-purpose silicone rubber with good flexibility and temperature resistance.
- FVMQ (Fluorosilicone) – Enhanced chemical and fuel resistance, ideal for aerospace and automotive applications.
- LSR (Liquid Silicone Rubber) – Ideal for injection molding, suitable for complex shapes and high-volume production.
- HTV (High-Temperature Vulcanized Silicone) – Solid silicone processed by compression or extrusion molding.
- RTV (Room Temperature Vulcanized Silicone) – Cures at room temperature, ideal for sealing, potting, and coating applications.
Type | Features | Common Applications |
---|---|---|
VMQ | General-purpose silicone rubber | Seals, gaskets, tubing |
FVMQ | Fuel/oil resistance, higher cost | Aerospace, automotive |
LSR | Liquid form, fast cure, complex parts | Medical devices, baby products |
HTV | High strength, molded parts | Gaskets, seals, keypads |
RTV | Easy application, room temp cure | Sealants, coatings |
What is the Raw Material of VMQ?
The raw materials for VMQ silicone rubber include:
- Silicon (Si) – Derived from quartz or sand.
- Dimethylsiloxane Monomers – Basic building block of PDMS.
- Vinyl Groups – Added for enhanced cross-linking and curing efficiency.
- Peroxide or Platinum Catalysts – Used in the curing process.
This unique chemical structure provides VMQ with its flexibility, thermal stability, and resistance to environmental factors.
What is the Hardness of VMQ Silicone?
The hardness of VMQ silicone typically ranges from 30 Shore A to 80 Shore A, depending on the specific formulation and curing process.
Is Silicone Harder Than Plastic?
No, silicone is generally softer than most rigid plastics. Silicone rubber is an elastomer with a flexible and rubbery texture, while plastic tends to be rigid and brittle in comparison.
Material | Hardness Range (Shore A/D) |
---|---|
VMQ Silicone | 30A – 80A |
Polypropylene (Plastic) | 70D – 80D |
Polycarbonate (Plastic) | 85D – 90D |
What are the Advantages and Disadvantages of Silicone Rubber?
🏆 Advantages of VMQ Silicone Rubber
✅ Advantage | 🔍 Description |
---|---|
🔥 High Temperature Resistance | Performs from -60°C to +200°C (higher for special grades). |
☀️ UV & Ozone Resistance | Excellent resistance to environmental aging. |
🧪 Chemically Inert | Non-reactive with most chemicals, suitable for medical use. |
👶 Biocompatible | Safe for medical and food contact applications. |
💧 Waterproof & Flexible | Excellent sealing and insulation properties. |
⚠️ Disadvantages of VMQ Silicone Rubber
❌ Disadvantage | 🔍 Description |
---|---|
🛢️ Poor Resistance to Fuels/Oils | Not recommended for use with petroleum-based oils or fuels. |
❄️ Low Tear Strength | Prone to mechanical tearing if not reinforced. |
💰 Cost | More expensive compared to other elastomers like NBR or EPDM. |
What is the Difference Between Silicone and Silicone Rubber?
Both silicone and silicone rubber are based on the same polysiloxane backbone but differ significantly in physical properties and industrial applications.
Silicone refers to a broad family of synthetic materials, while silicone rubber specifically refers to the cured, flexible elastomer used in seals, gaskets, and insulation components.
Material | Definition | Industrial Use |
---|---|---|
Silicone | A family of silicon-oxygen polymers, available as fluids, gels, resins, and elastomers. | Lubricants, adhesives, coatings, medical devices, and release agents. |
Silicone Rubber | A cured elastomer (rubber-like material) made from silicone polymers with cross-linking agents. | Seals, gaskets, O-rings, high-temperature insulation, tubing, and automotive parts. |
🔍 Key Differences
- ✅ Silicone rubber undergoes vulcanization or crosslinking, forming a flexible, durable material suitable for mechanical and sealing applications.
- ✅ Silicone (uncured) can be used as a fluid or gel, common in lubricants and adhesives.
- ✅ Silicone rubber delivers higher mechanical strength, elasticity, and thermal stability compared to uncured silicone.
What is the Maximum Temperature for Silicone Rubber?
One of the key reasons silicone rubber is preferred in industrial applications is its exceptional heat resistance.
Standard silicone rubber can handle continuous use from -60°C to +200°C. High-temperature grades can withstand temperatures up to +250°C, with short-term exposure limits reaching +300°C.
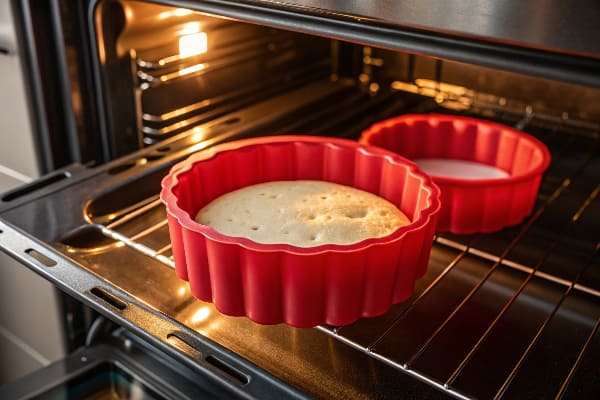
🔍 Temperature Performance Table
Silicone Rubber Type | Continuous Use Temperature | Peak Short-Term Temperature |
---|---|---|
Standard VMQ Silicone Rubber | -60°C to +200°C | Up to +250°C |
High-Temperature Grade Silicone | -60°C to +250°C | Up to +300°C |
Fluorosilicone (FVMQ) | -60°C to +230°C | Up to +260°C |
✅ Common Applications Requiring High-Temperature Silicone Rubber
- ✅ Automotive engine gaskets and turbocharger hoses
- ✅ Aerospace thermal insulation systems
- ✅ Industrial oven and furnace seals
- ✅ Electrical insulation in high-heat environments
What Temperature Does Rubber Melt At?
This is a common question for buyers selecting materials for thermal and mechanical stress environments. Rubber materials don’t “melt” in the conventional sense but decompose at high temperatures.
Silicone rubber does not have a melting point. It decomposes instead of melting, typically starting degradation at temperatures above +300°C. Other rubber types have much lower thermal stability.
🔍 Rubber Type Temperature Comparison Table
Rubber Type | Continuous Use Temperature | Decomposition Temperature |
---|---|---|
Natural Rubber (NR) | Up to +80°C | Decomposes from +200°C |
EPDM | Up to +150°C | Decomposes from +250°C |
Nitrile Rubber (NBR) | Up to +120°C | Decomposes from +250°C |
Silicone Rubber (VMQ) | Up to +250°C | Decomposes from +300°C |
Fluorosilicone (FVMQ) | Up to +230°C | Decomposes from +300°C |
FKM (Viton) | Up to +250°C | Decomposes from +350°C |
Practical Recommendations for Industrial Buyers
- ✅ For continuous high-heat applications above +200°C, choose silicone rubber or FKM materials.
- ✅ Ensure materials are certified for high-temperature use and compliant with ISO or FDA standards if necessary.
- ✅ Request thermal degradation data from suppliers for mission-critical applications.
What is Silicone Rubber Used For?
Silicone rubber (VMQ) is valued across industries for its flexibility, thermal stability, chemical resistance, and biocompatibility. It performs in environments where other materials fail, making it the preferred choice for both industrial and consumer products. In this section, I will explore the most important application areas in detail, including real use cases, key advantages, and why purchasing officers often choose silicone rubber in their projects.
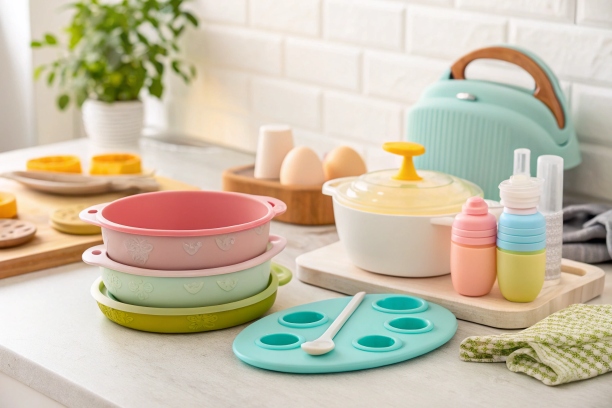
🏭 1. Automotive Industry
Silicone rubber is widely used in the automotive sector for components exposed to extreme temperature changes and harsh environments.
- ✅ Gaskets and Seals: VMQ silicone maintains sealing integrity from -60°C to +200°C, making it ideal for engine gaskets, valve cover seals, and O-rings in both combustion and electric vehicles.
- ✅ Hoses and Tubing: Silicone rubber is often used in radiator hoses and turbocharger hoses due to its heat resistance and flexibility.
- ✅ Electrical Insulation: Protects sensitive wiring and connectors from heat, vibration, and moisture in modern vehicles, including EV battery systems.
Why Automotive Manufacturers Prefer VMQ:
- ✅ No cracking under extreme temperature cycles
- ✅ Resistant to engine oils and coolants (certain grades)
- ✅ Longevity reduces maintenance costs and warranty claims
🏥 2. Medical and Healthcare Industry
VMQ silicone rubber’s biocompatibility and hypoallergenic nature make it suitable for a wide range of medical applications.
- ✅ Medical Tubing and Catheters: Flexible, non-reactive, and sterilizable, used in IV delivery and drainage systems.
- ✅ Implants: Breast implants, shunts, and cochlear implants rely on VMQ due to its inert properties.
- ✅ Seals and Stoppers: Used in syringe seals, IV bag closures, and pharmaceutical packaging to prevent contamination.
Compliance:
- ✅ Meets FDA 21 CFR 177.2600 for food and medical use
- ✅ USP Class VI certified for biocompatibility
- ✅ ISO 10993 approved for body contact
🍳 3. Food and Beverage Industry
Silicone rubber is a safe, durable, and flexible material for products that require repeated food contact and high-temperature resistance.
- ✅ Bakeware and Kitchen Tools: Muffin trays, spatulas, and baking mats made from food-grade silicone withstand temperatures up to 230°C without releasing harmful substances.
- ✅ Seals and Gaskets: Used in food processing machinery, beverage dispensers, and packaging lines to prevent leaks and contamination.
- ✅ Baby Products: Bottle nipples, pacifiers, and teething toys due to their softness, non-toxicity, and ease of sterilization.
Advantages for Food-Grade Applications:
- ✅ Tasteless and odorless, does not impart flavor
- ✅ Resistant to mold, bacteria, and degradation by UV
- ✅ Easy to clean and sterilize in commercial dishwashers or autoclaves
🔌 4. Electronics and Electrical Industry
Silicone rubber is extensively used to insulate and protect electrical components from temperature extremes, moisture, and dust.
- ✅ Keypads and Switch Covers: Soft-touch silicone provides excellent tactile feedback and weather protection in industrial control panels and consumer electronics.
- ✅ Insulation Sleeves: Protects wires in transformers, motors, and HVAC systems from thermal and electrical hazards.
- ✅ Potting and Encapsulation: Encases sensitive electronics to prevent corrosion and damage in automotive and outdoor equipment.
Performance Highlights:
- ✅ Withstands temperatures from -60°C to +200°C
- ✅ High dielectric strength and insulation properties
- ✅ Resistant to fire and low smoke emissions (certain grades)
🏗️ 5. Construction and Building Industry
Silicone rubber provides long-lasting sealing solutions in construction, offering resistance to UV, weathering, and temperature fluctuations.
- ✅ Window and Door Seals: Silicone-based seals maintain flexibility and air-tightness in building facades, curtain walls, and glass panels.
- ✅ Expansion Joints and Weather Seals: Absorbs structural movement in bridges, roads, and stadiums.
- ✅ Sealants: Applied in bathrooms, kitchens, and building exteriors for waterproofing and mold resistance.
Why Builders Choose VMQ:
- ✅ Does not degrade under UV or ozone exposure
- ✅ High elasticity allows for movement absorption
- ✅ Lifespan exceeds traditional rubber-based alternatives
🚀 6. Aerospace Industry
In aerospace, VMQ silicone’s performance at extreme altitudes and temperatures makes it an essential material for seals, gaskets, and vibration dampers.
- ✅ O-rings and Gaskets: Used in jet engines and pressurized cabins where high-temperature and fuel resistance are required.
- ✅ Thermal Insulation: Protects sensitive instruments from extreme cold and heat during flights and space missions.
- ✅ Vibration Dampers: Absorbs vibration and reduces noise in aircraft interiors and systems.
Benefits for Aerospace:
- ✅ Performs in environments from -60°C to +200°C
- ✅ Low outgassing and minimal weight increase
- ✅ Custom moldable for complex aerospace applications
🏭 Industry | 🔧 Common Applications | ✅ Key Benefits |
---|---|---|
Automotive |
|
|
Medical & Healthcare |
|
|
Food & Beverage |
|
|
Electronics & Electrical |
|
|
Construction & Building |
|
|
Aerospace |
|
|
Is VMQ Silicone Food Safe?
Yes, VMQ silicone is food safe when manufactured to comply with FDA and LFGB standards. Food-grade silicone is free from toxic additives and meets strict requirements for food contact safety.
Difference Between Food Grade Silicone and Regular Silicone
Type | Key Differences |
---|---|
Food Grade Silicone | Tested for purity, free from harmful chemicals, compliant with FDA/LFGB. |
Regular Industrial Silicone | May contain fillers or additives, not certified for food contact. |
What is the Difference Between VMQ and FVMQ?
VMQ and FVMQ are both silicone rubbers but differ in their chemical composition and performance.
Property | VMQ | FVMQ |
---|---|---|
Fluorinated Groups | No | Yes |
Fuel/Oil Resistance | Poor | Improved resistance to fuels and oils |
Temperature Range | -60°C to +200°C | -60°C to +230°C |
Cost | Lower | Higher |
Is VMQ Silicone Biocompatible?
Yes. VMQ silicone rubber is inherently biocompatible, making it suitable for use in medical devices, implants, and food-contact applications.
It meets various international biocompatibility standards, including:
- ✅ USP Class VI
- ✅ ISO 10993
- ✅ FDA 21 CFR 177.2600 (for food applications)
What Breaks Down Silicone Rubber?
Although VMQ silicone rubber is durable, certain factors can degrade it over time.
❌ Factor | ⚠️ Effect |
---|---|
Strong Acids and Alkalis | Chemical breakdown of polymer chains. |
High Energy Radiation | Causes cross-linking changes and embrittlement. |
Mechanical Stress | Tearing due to low tear strength. |
Prolonged Exposure to Petroleum Oils | Swelling and loss of mechanical properties. |
📞 Get a Free Quote or Sample of VMQ Silicone Rubber Products!
Looking for reliable VMQ silicone rubber gaskets, seals, or custom-molded components? We provide certified food-grade and medical-grade solutions tailored to your industry needs.
- ✅ Free samples available
- ✅ Fast production & on-time delivery
- ✅ ISO, RoHS, and FDA compliant materials
📧 Contact Kelly at Julong Rubber Today!
Email: info@rubberandseal.com
Website: www.rubberandseal.com
🔗 Explore Other Rubber Materials
The Manufacturing Process of Silicone Rubber Products
1. Formulation of Silicone Rubber Compound:
- The initial stage involves meticulously crafting a silicone rubber compound comprising a base silicone polymer, reinforcing fillers, crosslinking agents, and various additives, such as pigments and catalysts.
- The blend is engineered to yield specific mechanical properties – tensile strength, elongation, hardness, and thermal resistance. Proper formulation ensures that the compound meets the purchaser’s specifications.
2. Compound Mixing and Processing:
- The next step is the homogenization of the compound using high-shear mixers or two-roll mills.
- This step is critical for achieving a consistent and homogenous mix, eliminating air bubbles, and ensuring uniform dispersion of fillers.
3. Pre-forming and Calendaring:
- The mixed compound is then calendared into sheets or pre-formed into specific shapes to prepare for molding.
- The thickness and dimensions are closely monitored to minimize material wastage and ensure process efficiency.
4. Molding or Extruding:
There are various molding techniques for silicone rubber, including:
- Compression Molding: The mixed silicone material is placed in a heated mold, pressure is applied, and the silicone cures into the shape of the mold.
- Injection Molding: Liquid silicone rubber (LSR) is injected into a heated mold and cured.
- Transfer Molding: Similar to compression molding, but the silicone material is transferred into the mold cavity before being cured.
- Extrusion: The silicone rubber is forced through a die of the desired cross-section and then cured, often in a continuous process.
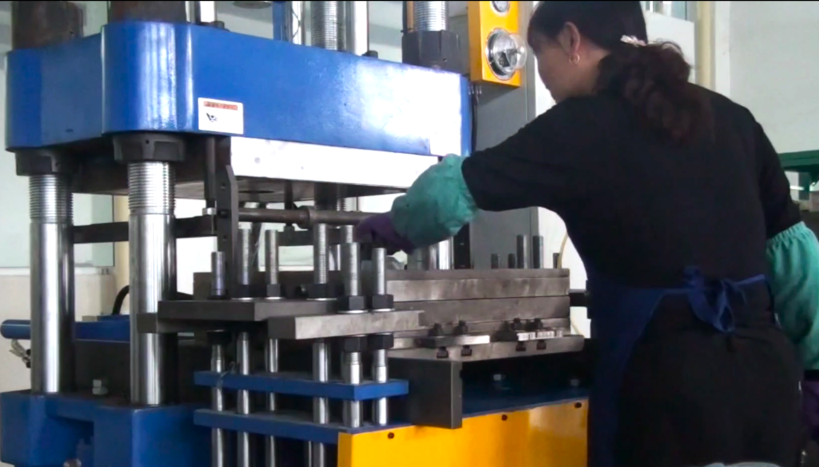
5. Curing or Vulcanization:
- Post-molding, the products undergo a curing process, typically in a heated press or oven.
- Vulcanization involves heating the product to a specific temperature under controlled conditions, facilitating cross-linking reactions that enhance the material’s properties.
6. Post-Curing Treatments:
- Products may require additional post-curing treatments to remove any residual by-products and improve mechanical properties.
- This step involves secondary heating in a clean environment, ensuring the product is compliant with stringent quality requirements.
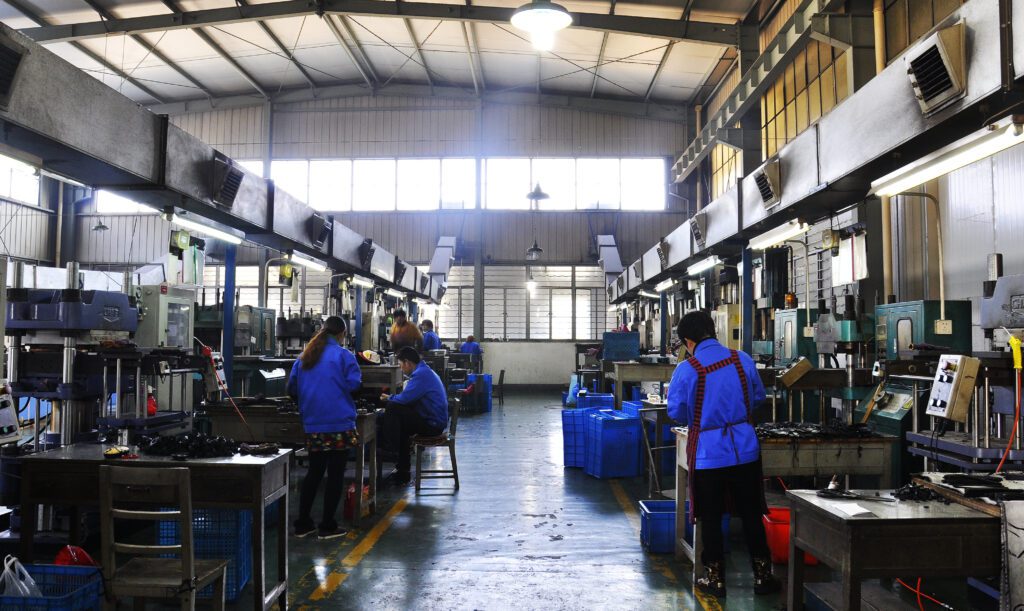
7. Secondary Operations and Finishing:
- Secondary operations include precision cutting, assembly, bonding, and surface treatments.
- These processes are tailored to meet the buyer’s specifications, ensuring functionalities like surface smoothness, dimensional accuracy, and assembly compatibility.
8. Quality Assurance and Testing:
- Rigorous testing ensures that the products meet or exceed the standards set by international certification bodies.
- Tests include tensile strength, elongation, compression set, and aging resistance, ensuring reliability and long-term performance.
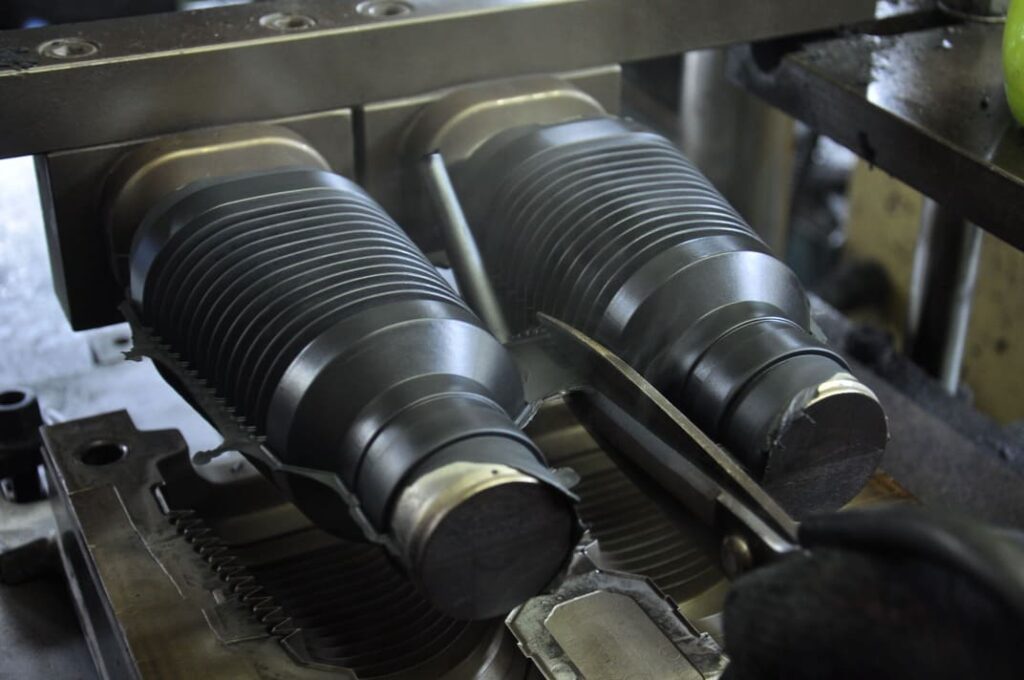
9. Packaging and Logistics:
- Finished products are carefully packaged to prevent damage during transit.
- Packaging materials and logistics solutions are selected to ensure product integrity and timely delivery.
10. Continuous Improvement and Feedback:
- Continuous feedback from customers drives improvements and innovations in the manufacturing process.
- Regular audits and feedback loops help optimize processes for cost-effectiveness and quality assurance.
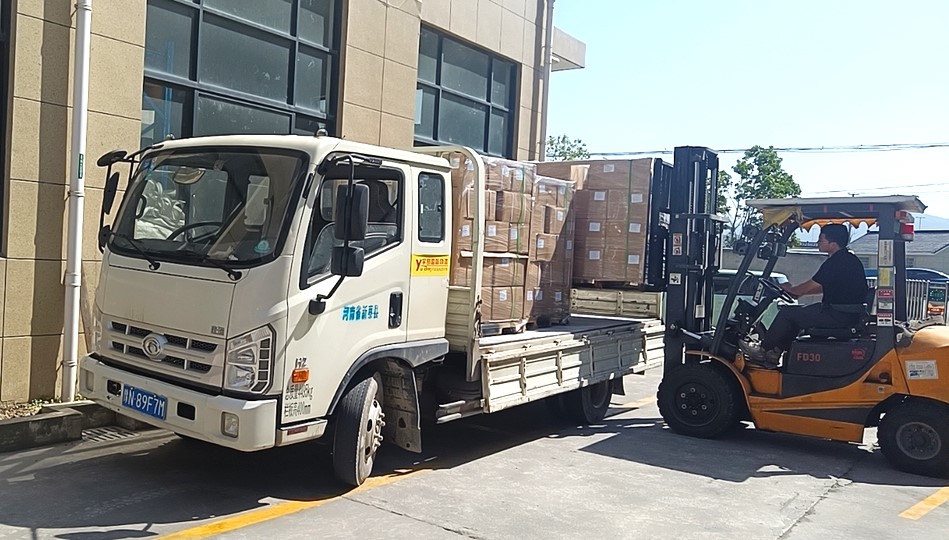
Custom Rubber Parts with Easy
At Julong Rubber, We turn complex Into Simple! Follow the following 3 steps to start today!

Tell Us What You Need
Tell us as specific as possible of your needs, provide the drawing, reference picture and share your idea.
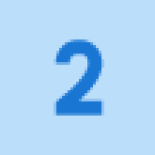
Get Solution & Quote
We will work on the best solution according to your requirements and drawing, the specific quote will be provided within 24 hours.

Approve for Mass Production
We will start mass production after getting your approval and deposit, and we will handle the shipment.
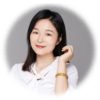
Get A Free Quote
Contact us to get a free quote and more expertise about custom rubber parts. Your project will meet the right solution at Julong Rubber.
Email:info@rubberandseal.com