Materials of Excellence
Crafting with the Best in the Business
At Julong Rubber, we prioritize using the finest materials to ensure the durability, efficiency, and performance of every product. Explore the various high-quality materials that form the foundation of our premium rubber components.
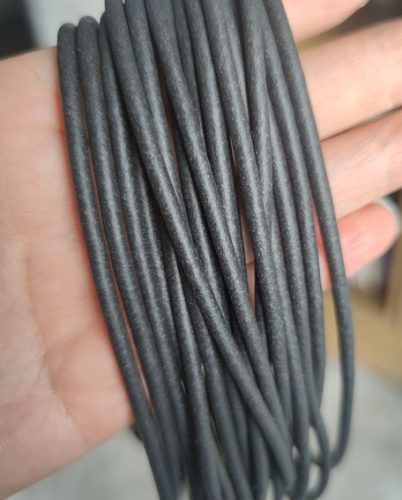
Sponge Rubber
The Versatile Cushioning Solution
Sponge rubber is a unique material, differentiated by its cellular structure which allows it to compress and rebound. This rubber type has a matrix of connected air pockets, which offers distinct cushioning characteristics. Because of its elasticity and resilience, sponge rubber has the ability to return to its original shape after compression. Depending on its formulation and the specifics of its manufacturing process, sponge rubber can be made soft or hard, and with closed or open cells.
Sponge Rubber: Applications,and Selection Guide
Sponge rubber is an essential material used in various industrial applications due to its flexibility, lightweight nature, and excellent sealing properties. For B2B procurement professionals, understanding sponge rubber’s applications, advantages, and selection criteria ensures better decision-making in sourcing industrial seals, gaskets, and insulation components.
This comprehensive guide covers everything from the types and benefits of sponge rubber to industry-specific applications and detailed comparison with solid rubber materials.
What is Sponge Rubber?
Sponge rubber is a type of cellular rubber composed of either open-cell or closed-cell structures. It is known for its compressibility, cushioning, and excellent sealing capability against air, dust, water, and sound.
Sponge rubber is a lightweight, flexible elastomer with a porous structure, offering superior cushioning, insulation, and sealing performance in various industrial and commercial applications.
Types of Sponge Rubber
Sponge rubber can be classified into different types based on material composition and cell structure. Each type offers unique properties suited to specific applications.
🔍 Cell Structure Types
- ✅ Open-Cell Sponge Rubber: Features interconnected cells that allow air and moisture to pass through. Commonly used for cushioning and sound absorption.
- ✅ Closed-Cell Sponge Rubber: Contains discrete, non-interconnected cells that prevent the passage of air, water, and gases. Ideal for sealing and insulation.
🔍 Material Types
Material | Structure | Key Properties | Common Applications |
---|---|---|---|
EPDM Sponge Rubber | Closed-Cell | Weather, ozone, and UV resistant | Outdoor seals, HVAC gaskets |
Silicone Sponge Rubber | Closed-Cell | High-temperature resistance, FDA compliant | Food processing, medical equipment |
Neoprene Sponge Rubber | Closed-Cell | Oil, chemical, and flame resistant | Marine, automotive seals |
Nitrile Sponge Rubber | Closed-Cell | Oil and fuel resistant | Fuel tank seals, industrial gaskets |
What are the Advantages and Disadvantages of Sponge Rubber?
Sponge rubber offers a unique set of properties that make it suitable for many industrial applications. However, like all materials, it comes with both strengths and limitations.

✔️ Advantages of Sponge Rubber
1. Excellent Sealing Capability
Sponge rubber, particularly closed-cell variants, provides an effective barrier against water, dust, gases, and air. It compresses easily to fill gaps, making it ideal for sealing applications in automotive, HVAC, and industrial machinery.
2. Lightweight and Flexible
Due to its cellular structure, sponge rubber is significantly lighter than solid rubber. This makes it suitable for applications where reducing weight is critical, such as transportation and aerospace components.
3. Superior Cushioning and Shock Absorption
Sponge rubber’s structure absorbs shocks and vibrations effectively, protecting sensitive equipment and reducing noise in industrial and automotive applications. It improves ergonomics by providing cushioning in products like grips, handles, and gaskets.
4. Thermal and Acoustic Insulation
The closed-cell structure traps air, providing excellent thermal insulation properties. Additionally, its sound-absorbing qualities make it an ideal choice for noise reduction in HVAC systems and construction.
5. Resistance to Environmental Factors
Depending on the type of rubber used, sponge rubber can offer resistance to UV rays, ozone, extreme temperatures, and weathering. For example, EPDM sponge rubber performs well outdoors, while silicone sponge rubber can withstand high-temperature environments up to +250°C.
6. Customizable Density and Hardness
Manufacturers can tailor the density (hardness) and cell structure to specific applications, ranging from soft, highly compressible materials to firmer, more durable formulations.
❌ Disadvantages of Sponge Rubber
1. Lower Mechanical Strength Compared to Solid Rubber
While sponge rubber is flexible and lightweight, it lacks the tensile strength and durability of solid rubber. It’s not suitable for applications requiring high tear resistance, heavy mechanical loads, or constant abrasion.
2. Limited Load-Bearing Capacity
Sponge rubber’s compressibility, although beneficial for sealing, limits its ability to bear heavy static or dynamic loads. Over-compression can lead to permanent deformation (compression set), reducing sealing effectiveness over time.
3. Open-Cell Variants Absorb Moisture
Open-cell sponge rubber, although breathable and cushioning, can absorb water and other fluids. This limits its use in outdoor or wet environments unless sealed or coated properly.
4. Cost Variability Based on Material Type
High-performance sponge rubbers like silicone and fluorosilicone are significantly more expensive than standard neoprene or EPDM sponges. This can increase material costs in projects with tight budgets.
5. Chemical Compatibility Limitations
Not all sponge rubbers are resistant to oils, fuels, or aggressive chemicals. For instance, EPDM sponge rubber performs poorly in oil and fuel environments, requiring nitrile or fluorocarbon-based alternatives for such applications.
🔧 Advantages vs Disadvantages at a Glance
Feature | Advantage | Disadvantage |
---|---|---|
Sealing Performance | Excellent for air, water, and dust | Compression set may occur over time |
Flexibility | Highly flexible and compressible | Limited structural support |
Weight | Lightweight, reduces overall weight | Not suitable for load-bearing applications |
Thermal Insulation | Effective in temperature control applications | Open-cell types may absorb moisture and lose insulation properties |
Cost | Cost-effective for EPDM and neoprene sponges | High-end types like silicone can be costly |
🔎 When to Choose Sponge Rubber
- ✅ Applications requiring effective sealing in light to moderate conditions (HVAC, automotive seals)
- ✅ Projects needing cushioning and noise reduction without adding excessive weight
- ✅ Environments where flexibility and compression are more important than mechanical strength
❗ When Not to Choose Sponge Rubber
- ❌ Heavy load-bearing applications that demand high tensile strength
- ❌ Environments with aggressive oils, fuels, or chemicals not compatible with specific sponge rubber types
- ❌ Applications where long-term compression resistance is critical without risk of compression set
Application of Sponge Rubber
Sponge rubber is used in industries requiring lightweight, compressible sealing and insulation materials. Below is a deep dive into industry-specific applications with technical insights.
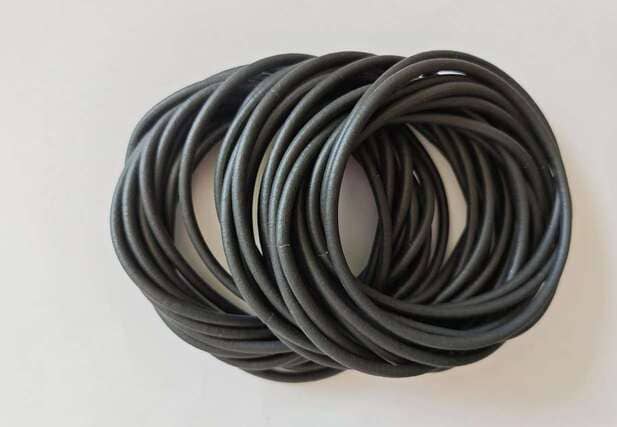
🚗 Automotive Industry
- ✅ Applications: Door seals, trunk seals, weather stripping, HVAC seals.
- ✅ Technical Benefits:
- Closed-cell EPDM sponge resists weather and UV degradation.
- Reduces road noise and vibration inside the cabin.
- Prevents water and dust intrusion in vehicle compartments.
🔧 Automotive Sealing Comparison
Material | Weather Resistance | Noise Reduction | Seal Integrity |
---|---|---|---|
EPDM Sponge | Excellent | High | Excellent |
Neoprene Sponge | Good | Moderate | Good |
Silicone Sponge | Excellent | Moderate | Excellent |
🏢 Construction and HVAC Industry
- ✅ Applications: Window and door gaskets, HVAC duct seals, expansion joint fillers.
- ✅ Technical Benefits:
- Reduces energy loss through air leaks in HVAC systems.
- Prevents water penetration and noise ingress in buildings.
- UV-resistant EPDM and silicone sponge last longer in outdoor conditions.
🔧 Sealing Material Performance in Construction
Material | Thermal Insulation | Water Resistance | Weatherability |
---|---|---|---|
EPDM Sponge | Good | Excellent | Excellent |
Neoprene Sponge | Moderate | Good | Good |
Silicone Sponge | Excellent | Good | Excellent |
🏥 Medical and Food Processing Industry
- ✅ Applications: Sterilizer gaskets, oven seals, food processing equipment seals.
- ✅ Technical Benefits:
- FDA-approved silicone sponge ensures hygiene and safety.
- Performs in high-temperature sterilization environments.
- Non-toxic and odorless materials ensure compliance with medical standards.
🔧 Material Comparison for Food & Medical Applications
Material | FDA Compliance | Temperature Resistance | Cleanability |
---|---|---|---|
Silicone Sponge | Yes | Up to +250°C | Excellent |
EPDM Sponge | No | Up to +150°C | Good |
Neoprene Sponge | No | Up to +120°C | Good |
What is the Difference Between Sponge Rubber and Solid Rubber?
- ✅ Density: Sponge rubber is lightweight with a cellular structure; solid rubber is denser and heavier.
- ✅ Compression: Sponge rubber compresses easily and is ideal for sealing; solid rubber is stiffer and provides structural support.
- ✅ Applications: Sponge rubber is used for gaskets and seals requiring flexibility; solid rubber is used for vibration mounts and heavy-duty applications.
🔧 Comparative Table
Feature | Sponge Rubber | Solid Rubber |
---|---|---|
Density | Low | High |
Compression | High | Low |
Application | Sealing, Insulation | Structural, Impact Resistance |
How to Choose Sponge Rubber?
For B2B buyers, choosing the right sponge rubber involves understanding the application environment and performance requirements. Here’s a step-by-step guide.
🔍 Step 1: Define the Application Requirements
- ✅ Sealing, cushioning, or insulation needs.
- ✅ Exposure to UV, ozone, oils, fuels, or chemicals.
- ✅ Compression and recovery requirements.
🔍 Step 2: Select the Cell Structure
- ✅ Open-Cell Sponge: For sound absorption and cushioning.
- ✅ Closed-Cell Sponge: For sealing against liquids, dust, and air.
🔍 Step 3: Match the Material to the Environment
Material | Temperature Range | Key Applications |
---|---|---|
EPDM Sponge | -40°C to +150°C | Outdoor seals, HVAC gaskets |
Silicone Sponge | -60°C to +250°C | Food, medical, high-temperature seals |
Neoprene Sponge | -20°C to +120°C | Marine, automotive seals |
🔍 Step 4: Verify Compliance and Standards
- ✅ ISO 9001 certified quality management.
- ✅ RoHS and REACH compliance.
- ✅ FDA approval for food and medical applications (if required).
📞 Get a Free Quote or Sample of Sponge Rubber Products!
At Julong Rubber, we manufacture high-performance sponge rubber gaskets, seals, and insulation products for industrial applications. Our team provides custom solutions tailored to your needs.
- ✅ Free technical consultation and samples.
- ✅ ISO 9001 certified production with short lead times.
- ✅ Global delivery and competitive pricing for B2B buyers.
📧 Contact Kelly at Julong Rubber Today!
Email: info@rubberandseal.com
Website: www.rubberandseal.com
🔗 Explore Other Rubber Materials
Custom Rubber Parts with Easy
At Julong Rubber, We turn complex Into Simple! Follow the following 3 steps to start today!

Tell Us What You Need
Tell us as specific as possible of your needs, provide the drawing, reference picture and share your idea.
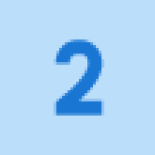
Get Solution & Quote
We will work on the best solution according to your requirements and drawing, the specific quote will be provided within 24 hours.

Approve for Mass Production
We will start mass production after getting your approval and deposit, and we will handle the shipment.
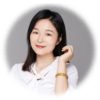
Get A Free Quote
Contact us to get a free quote and more expertise about custom rubber parts. Your project will meet the right solution at Julong Rubber.
Email:info@rubberandseal.com