Struggling with frequent replacements due to worn-out rubber parts? Abrasion resistance is critical when choosing rubber for industrial applications. Selecting the wrong material could lead to costly downtime and unnecessary replacements. Let me help you navigate this essential choice with confidence and insight.
The best rubber for abrasion resistance is:
Each material offers specific benefits: polyurethane for toughness, nitrile for durability in oily environments, and natural rubber for flexibility in various settings. Always match the material to your specific application needs.
Understanding this is just the start. Let’s dive into the details to help you make the perfect choice.
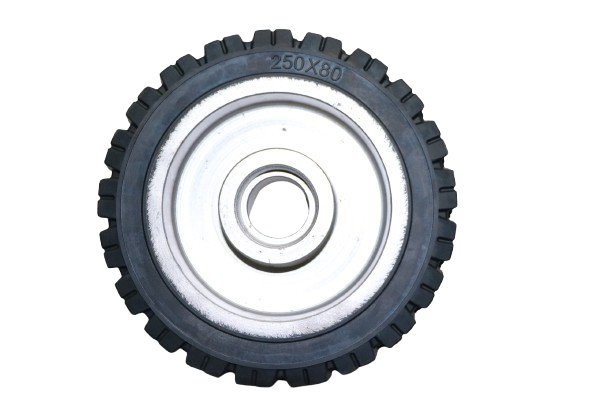
Why Does Abrasion Resistance Matter?
Abrasion resistance determines how well rubber withstands wear and tear during usage. Applications like conveyor belts, rubber wheels, and gaskets demand materials that can handle constant friction. Without it, your operation may face unnecessary delays, increased costs, and customer dissatisfaction.
Which Rubber Materials Are the Most Abrasion-Resistant?
Here’s a breakdown of the top contenders:
Neoprene
- Advantages: Durable, waterproof, resistant to oils and chemicals.
- Best Applications: Wetsuits, gaskets, seals, and automotive hoses.
- Learn more about neoprene benefits.
Nitrile
- Advantages: Excellent oil resistance, durable, high abrasion resistance.
- Best Applications: Fuel hoses, gaskets, seals, and O-rings.
- Learn more about nitrile benefits.
Natural Rubber
- Advantages: High elasticity, good tensile strength, cost-effective.
- Best Applications: Tires, shock absorbers, and rubber bands.
- Learn more about natural rubber benefits.
Viton
- Advantages: Exceptional heat resistance, chemical resistance, long-lasting.
- Best Applications: Seals for automotive and aerospace applications, gaskets for chemical processing.
- Learn more about Viton benefits.
EPDM
- Advantages: Excellent weather resistance, good thermal stability, ozone resistance.
- Best Applications: Roofing membranes, automotive weather stripping, and electrical insulation.
- Learn more about EPDM benefits.
Polyurethane Rubber
Known for exceptional abrasion resistance. Its toughness makes it ideal for high-impact environments like mining or heavy machinery.
- Advantages: Tough, durable, resistant to cuts.
- Best Applications: Conveyor belts, forklift wheels, and bushings.
- Learn more about polyurethane benefits.
What Factors Affect Abrasion Resistance?
Not all abrasion-resistant rubbers are created equal. Key factors include:
- Durometer (Hardness)
Softer rubber may wear faster under heavy loads, while harder materials resist abrasion better.
Understand durometer scales. - Friction Levels
Applications with high friction demand tougher materials like polyurethane. - Chemical Exposure
Oils and chemicals can weaken some rubbers. Nitrile shines in these settings. - Temperature Conditions
Extreme temperatures can affect performance. Ensure the rubber suits your operational environment.
How to Choose the Right Rubber for Your Needs?
Answering these questions will guide your decision:
- Is your application exposed to oils or fuels?
- Will the rubber face high friction or impact?
- What are the operating temperatures?
- Do you need flexibility or rigidity?
Matching these factors to a rubber type ensures long-lasting performance and fewer replacements.
Real-Life Applications: Matching Rubber to Industry
Let’s look at examples to make this clear:
- Conveyor Belts in Mining
Use polyurethane for its ability to handle constant friction and heavy loads. - Gaskets for HVAC Systems
Nitrile rubber excels here due to its oil resistance and flexibility. - Industrial Rollers
Natural rubber works best for its elasticity and cost-effectiveness.
Tips for Maximizing Abrasion Resistance
- Regular Inspections: Check for signs of wear and replace damaged parts promptly.
- Custom Solutions: Consider customized rubber profiles for better performance.
- Certification: Look for materials with proven certifications.
Common Misconceptions About Abrasion-Resistant Rubber
- "Harder is always better." Not true! The right balance between hardness and flexibility matters.
- "All rubbers resist oil equally." Only materials like nitrile excel in oily settings.
Final Thoughts
Choosing the best rubber for abrasion resistance depends on your application. Whether it’s polyurethane for durability, nitrile for oil resistance, or natural rubber for flexibility, selecting the right material saves time, money, and effort.
Have questions or need tailored advice? Reach out to our team of experts at Julong Rubber. We specialize in customized solutions that ensure top-quality performance.
Summary: Abrasion resistance is vital for industrial applications. From polyurethane to natural rubber, understanding your options helps ensure durability and efficiency. Contact us for customized solutions to fit your needs.