Are you wondering why industrial rubber plays such a critical role in manufacturing? This versatile material is integral to a wide range of industries, offering benefits like durability, flexibility, and reliability in tough conditions.
Industrial rubber is essential in manufacturing due to its unique properties such as flexibility, durability, and resistance to wear. It is used in everything from seals and gaskets to conveyor belts and hoses.
Rubber’s versatility and performance make it indispensable in various manufacturing processes. Let’s dive into the key reasons why industrial rubber is a crucial material in modern manufacturing and the diverse applications it serves.
What Is Industrial Rubber?
Before we explore why industrial rubber is so vital, it’s important to understand what it actually is and how it differs from other types of rubber materials.
Industrial rubber is a synthetic or natural elastomer used for a variety of industrial applications. It is specifically engineered to withstand harsh environments, chemicals, heat, and mechanical stress.
Industrial rubber1 refers to rubber materials that are specifically formulated for industrial applications. These rubbers are often designed to perform under demanding conditions, such as high pressure, extreme temperatures, or exposure to chemicals. There are two main types of industrial rubber:
Natural Rubber2: Derived from the latex of rubber trees, natural rubber is known for its high elasticity and resilience. It is commonly used in applications that require a material that can stretch and recover, such as in seals, gaskets, and hoses.
Synthetic Rubber3: This is manufactured from petroleum-based monomers and includes a variety of compounds like nitrile rubber (NBR), EPDM, neoprene, and more. Synthetic rubbers are often tailored to meet specific requirements like oil resistance, heat resistance, and chemical compatibility.
Industrial rubber is used in many critical components across industries such as automotive, aerospace, medical, and food processing. Its flexibility, durability, and ability to withstand environmental stress make it indispensable for creating high-performance products.
Rubber Type | Key Features | Common Applications |
---|---|---|
Natural Rubber | High elasticity, excellent resilience | Seals, gaskets, hoses |
Synthetic Rubber | Customizable for specific needs | Automotive parts, belts, coatings |
✅ Why it matters:
Industrial rubber provides the perfect balance of flexibility, strength, and longevity for critical components in manufacturing processes across a wide variety of sectors.
Why Is Industrial Rubber Important in Manufacturing?
What makes industrial rubber so valuable in the manufacturing industry? The unique properties of rubber make it a key material in the creation of durable, reliable components.
Industrial rubber is crucial in manufacturing due to its excellent flexibility, durability, resistance to chemicals, and ability to withstand extreme temperatures. It is used in everything from seals and gaskets to industrial machinery parts.
Industrial rubber is vital to manufacturing for several key reasons:
Flexibility and Resilience4: Rubber’s flexibility allows it to stretch and return to its original shape. This makes it ideal for components like seals, gaskets, and hoses that need to maintain a tight fit under fluctuating pressures and temperatures.
Durability5: Rubber is resistant to wear and tear, making it a long-lasting material. In manufacturing, components that need to endure repeated movement or contact, like belts, seals, and O-rings, often rely on rubber’s durability.
Resistance to Chemicals and Oils6: Certain types of rubber, such as nitrile rubber, are resistant to oils, fuels, and chemicals. This property makes rubber ideal for automotive, aerospace, and industrial applications that involve exposure to harsh chemicals or oils.
Temperature Resistance: Some rubber compounds, such as EPDM and silicone rubber, can withstand high temperatures, making them ideal for applications like engine seals, HVAC systems, and other high-heat environments.
Shock Absorption and Vibration Dampening: Rubber is an excellent material for absorbing shocks and vibrations. Components like rubber bushings, mounts, and grommets are used in industrial machinery, vehicles, and electronic devices to reduce wear and noise.
Key Benefits of Industrial Rubber:
Benefit | Explanation | Example Applications |
---|---|---|
Flexibility | Allows parts to stretch and return to original shape | Seals, hoses, gaskets |
Durability | Resistant to wear and tear | Conveyor belts, rollers |
Chemical Resistance | Protects against oils, chemicals, and fuels | Fuel hoses, oil seals |
Temperature Resistance | Withstands extreme heat or cold | Engine parts, HVAC seals |
Shock Absorption | Absorbs vibrations and impacts | Bumpers, mounts, grommets |
✅ Why it matters:
These properties make industrial rubber a cornerstone of modern manufacturing, ensuring that components perform reliably under harsh conditions, enhancing product longevity, and minimizing downtime.
What Are the Most Common Applications of Industrial Rubber?
Are you curious about where industrial rubber is used? Let’s explore the most common applications of rubber in manufacturing and why it’s indispensable in those areas.
Industrial rubber is used in a wide variety of manufacturing applications, including automotive parts, gaskets, seals, hoses, belts, and vibration-dampening components.
Industrial rubber is found in many critical manufacturing applications, including:
Automotive Industry7: Rubber is used in seals, gaskets, hoses, belts, and tires. It helps prevent leaks, reduce vibration, and ensure the durability of automotive components.
Industrial Equipment: Rubber components like seals, gaskets, and vibration dampers are used in machinery to prevent damage from movement, temperature fluctuations, and chemical exposure.
Medical Devices8: Rubber is used in seals, tubes, and gloves for medical applications. Medical-grade rubber is biocompatible and resistant to contamination, making it essential for sterile environments.
Construction and HVAC: Rubber is used for seals in doors and windows, as well as in HVAC systems for vibration dampening and weatherproofing.
Food and Beverage Industry9: Food-grade rubber is used in seals, gaskets, and hoses for food processing equipment. Its non-toxic, easy-to-clean properties make it ideal for these applications.
Industry | Rubber Applications | Key Components |
---|---|---|
Automotive | Seals, hoses, gaskets, belts, tires | O-rings, engine seals, tires |
Industrial Equipment | Seals, gaskets, vibration dampers | Conveyor belts, rollers |
Medical | Tubes, seals, gloves | Catheters, syringes, seals |
Construction & HVAC | Weatherproofing, vibration dampening | Seals, HVAC components |
Food & Beverage | Seals, gaskets, hoses | Food-safe hoses, seals |
✅ Why it matters:
Industrial rubber’s versatility across industries makes it a go-to material for ensuring durability, safety, and reliability in manufacturing processes.
What Are the Types of Rubber Used in Manufacturing?
Are you curious about which types of rubber are best suited for different manufacturing applications? Let's break down the most common types of industrial rubber and their unique characteristics.
The most common types of industrial rubber include natural rubber, EPDM, neoprene, nitrile, and silicone. Each type offers specific benefits for different applications.
There are various types of rubber used in industrial manufacturing, each offering unique properties to meet specific needs:
Natural Rubber10: Known for its high elasticity, natural rubber is ideal for applications requiring flexibility and resilience, such as seals and gaskets.
EPDM Rubber11: Ethylene Propylene Diene Monomer (EPDM) is highly resistant to weather, ozone, and aging, making it ideal for outdoor applications like roofing seals and gaskets in automotive and HVAC systems.
Neoprene Rubber: Neoprene offers good resistance to oil, weather, and aging. It’s commonly used in seals, gaskets, and belts.
Nitrile Rubber (NBR)12: Known for its excellent resistance to oils, fuels, and solvents, nitrile rubber is used in seals and gaskets in the automotive and industrial sectors.
Silicone Rubber: Silicone rubber is highly resistant to extreme temperatures, both high and low. It’s commonly used in medical devices, food processing, and automotive applications.
Rubber Type | Key Properties | Common Applications |
---|---|---|
Natural Rubber | High elasticity, good resilience | Seals, gaskets, hoses |
EPDM Rubber | Weather, ozone, and aging resistance | Automotive gaskets, roofing |
Neoprene Rubber | Oil, weather, and aging resistance | Seals, gaskets, belts |
Nitrile Rubber | Excellent oil and fuel resistance | Automotive, industrial seals |
Silicone Rubber | High-temperature resistance, biocompatible | Medical devices, food-safe seals |
✅ Why it matters:
Choosing the right type of rubber for a specific application is crucial for ensuring product performance and durability. Each type of rubber offers distinct benefits depending on environmental conditions and requirements.
Conclusion
Industrial rubber is crucial in manufacturing because of its versatility, durability, and resistance to wear, chemicals, and temperature extremes. From automotive to medical applications, rubber parts ensure efficient performance, safety, and longevity. The various types of industrial rubber, such as natural rubber, EPDM, and silicone, are tailored for different applications, making rubber indispensable in modern manufacturing processes.
🚀 Need Custom Rubber Solutions for Your Manufacturing Needs?
Contact Julong Rubber today or Request a Custom Quote for high-quality rubber components tailored to your specifications!
Or reach out to us directly via WhatsApp:
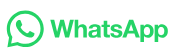
Explore the unique properties and advantages of industrial rubber that make it essential in various manufacturing processes. ↩
Discover the characteristics of natural rubber and its critical applications in industrial settings. ↩
Learn about the various types of synthetic rubber and how they are tailored for specific industrial needs. ↩
Understanding the benefits of flexibility and resilience in industrial rubber can enhance your manufacturing processes and product quality. ↩
Exploring the importance of durability in industrial rubber can help you choose the right materials for long-lasting components. ↩
Learning about chemical resistance in industrial rubber can guide you in selecting materials for harsh environments, ensuring safety and efficiency. ↩
Explore this link to understand how rubber enhances safety and performance in vehicles, crucial for automotive innovation. ↩
Discover the importance of rubber in medical applications, ensuring safety and sterility in healthcare environments. ↩
Learn about the critical role of food-grade rubber in maintaining hygiene and safety in food processing. ↩
Explore the unique properties of Natural Rubber and its applications to understand its importance in manufacturing. ↩
Learn about EPDM Rubber's resistance to weather and aging, crucial for outdoor durability in various industries. ↩
Discover how Nitrile Rubber's oil resistance enhances performance in automotive and industrial sectors. ↩